Hangzhou Normal University: The Impact of MAPE on the Friction and Wear Properties of PA66/PTFE Blends
Engineering Plastics Applications
2025-04-01 11:11:19
The melt blending method was employed to prepare maleic anhydride-grafted polyethylene (MAPE) modified polyamide 66/polytetrafluoroethylene (PA66/PTFE) blends. Under unlubricated conditions, the friction and wear properties of the materials under different loads were tested using a three-pin-on-disk friction test method. The fracture surfaces and wear morphologies of the materials were characterized by scanning electron microscopy (SEM), and the wear mechanisms were analyzed. The results showed that the addition of PTFE alone could improve the self-lubricating properties of PA66, but the friction coefficient exhibited significant fluctuations, along with an increased volumetric wear rate. When MAPE was used to replace PTFE under a fixed total additive mass fraction of 20%, the friction coefficient of the material further decreased, and the wear resistance was significantly improved, demonstrating a certain synergistic friction-reducing effect. Compared to PA66/MAPE (80/20) and PA66/PTFE (80/20), PA66/PTFE/MAPE (80/5/15) exhibited the lowest friction coefficient of 0.234, a 55.3% reduction compared to pure PA66 (0.523), and a volumetric wear rate of 3.23×10−6 mm3/(N∙m), a 44.1% decrease compared to pure PA66. In long-distance, multi-stage friction tests, except for pure PA66, all modified materials showed a gradual decrease and stabilization in the volumetric wear rate per unit distance as the sliding distance increased. Among them, the PA66/PTFE/MAPE blend exhibited the lowest and most stable friction coefficient, along with the smallest overall volumetric wear rate. SEM images of the wear surfaces revealed that MAPE enhanced the interaction between the PA66 matrix and PTFE, reducing the width of wear scars and improving wear resistance. Friction test results under different loads further confirmed the synergistic friction-reducing effect of MAPE and PTFE on PA66 materials.
Polyamide 66 (PA66) is an engineering plastic that can replace metals and is used in automotive components, mechanical manufacturing, and other fields, offering advantages such as high mechanical strength and good processing performance [1-3]. It can be used to manufacture parts like gears and bearings [4-8]. However, in the absence of lubrication, PA66 exhibits a high coefficient of friction and low wear resistance [9], particularly under extreme operating conditions, especially in special scenarios where the use of lubricating oil/grease is prohibited, such as in the aerospace industry [10-11], which imposes higher requirements for its self-lubricating and wear-resistant properties.
Polytetrafluoroethylene (PTFE) is an organic solid lubricant commonly used for improving the wear resistance and self-lubrication of polymer materials. During sliding, it can form a thin film layer on its surface and the mating surface, resulting in a low coefficient of friction. According to Li et al., under low load and low-speed conditions, PTFE/copper composites form a thin and uniform transfer film on the GCr15 mating surface, but the adhesion between the transfer film and the steel ring is weak, and a continuous transfer film is lacking. Due to PTFE's extreme inertness and weak intermolecular forces, its compatibility with the polymer matrix is poor, making it difficult to improve the material's wear resistance. Therefore, the compatibility between PTFE and the matrix must be enhanced. Li et al. reported that the use of reactive graft copolymers, such as maleic anhydride (MAH) grafted polytetrafluoroethylene (PTFE-g-MAH), can effectively increase the interfacial adhesion between polyamide 6 (PA6) and PTFE, enhancing the tribological properties and tensile strength of PA6/PTFE-g-MAH blends. However, due to PTFE's high melt processing temperature, the preparation of PTFE-g-MAH is challenging.
Polyethylene (PE) has a non-polar chain structure similar to PTFE. Due to its low intermolecular forces and inherent molecular chain flexibility, it can also serve as a solid lubricant in polymer-based wear-resistant and self-lubricating materials [19-22]. Jin et al. [23] found that adding just 2.0 wt% of ultra-high molecular weight polyethylene (PE-UHMW) to a PEEK matrix reduced the coefficient of friction and wear rate by 61% and 89%, respectively. Keresztes et al. [24] observed that PE-filled cast PA6 significantly improved the wear resistance of PA6. Moreover, the compatibility between PE and polyamide matrices can be easily enhanced through surface modification, leading to more uniform dispersion of PE particles and further potential improvement in friction performance. Wang et al. [25] prepared PA66/PE-UHMW composites compatibilized with maleic anhydride (MAH)-grafted high-density polyethylene (PE-HD-g-MAH) and found that the coefficient of friction decreased noticeably with increasing PE-UHMW content.
Currently, improvements in the friction and wear properties of PA66 are mainly focused on fiber reinforcement [26-27] and lubricant modification [28-29], among others; however, there is limited reporting on the impact of maleic anhydride grafted polyethylene (MAPE) on the friction and wear properties of PA66/PTFE blends. Considering the similarity in nonpolar structures between PE and the solid lubricant PTFE, as well as their adaptability to functionalization, this study primarily investigates the effect of MAPE on the friction and wear properties of PA66/PTFE blends and their wear mechanisms.
PA66: 101 F, DuPont Company, USA.
MAPE: HAD-14A, grafting rate 0.8%~1.0%, Nanhai Bochen High Polymer New Materials Co., Ltd.
PTFE: M1300, particle size 5~10 μm, DuPont, USA;
Xylene and Ethanol: Shanghai Guoyao Group Chemical Reagent Co., Ltd.
1.2 Main Instruments and Equipment
Twin-screw extruder: TSE-30A/500-11-40, Nanjing Ruiya Extrusion Group Co., Ltd.
Injection molding machine: SA600Ⅱ/130, Ningbo Haitian Plastic Machinery Group Co., Ltd.;
Electronic Universal Testing Machine: UTM4204, Zhuhai SANS Testing Equipment Co., Ltd.
Impact Testing Machine: DR-6025A, Yangzhou Derui Instrument Equipment Co., Ltd.
Friction and Wear Testing Machine: MMW-1A, Jinan Yihua Tribology Testing Technology Co., Ltd.;
Scanning Electron Microscope (SEM): sigma500, by Carl Zeiss company.
Electric Heating Air Blast Drying Oven: DHG-9140A, Shanghai Jing Hong Laboratory Equipment Co., Ltd.
Using a twin-screw extruder, PA66 was melt-blended with PTFE and MAPE. The sample codes and specific mass fractions of each component are shown in Table 1. The screw speed was 300 r/min, and the temperature was 270 ℃. Test strips were prepared through injection molding, with the injection temperature set at 270 ℃.
Table 1 Sample Code and Mass Fraction of Each Component %
1.4 Testing and Characterization
Friction tests in the pin-on-disc mode were conducted under dry sliding conditions on a tribometer, following the ASTM G 99-2017 standard. The test load was varied, with a friction coefficient test speed (v) of 120 r/min. The wear height change (∆h) before and after testing for each sample was measured and calculated, and the wear volume (∆V) was computed. The volumetric wear rate was then determined.
The calculation formula for [mm3/(N∙m)] is shown in Equation (1).
|
 |
(1) |
Where: ∆V is the wear volume, mm³; P is the load, N; L is the sliding distance, m.
Use a universal testing machine to test the flexural and tensile properties of materials according to GB/T 9341-2008 and GB/T 1040.2-2006, with a testing speed of 20 mm/min.
Using a impact testing machine, the impact strength of the material was tested according to GB/T 1043-1993.
Dynamic thermomechanical analysis was performed in a three-point bending configuration, with a frequency of 1 Hz, a heating rate of 5 °C/min, and a temperature range of 25 to 180 °C.
The morphology of the material's worn surface and impact fracture was observed using SEM. Prior to characterization, the sample fracture was etched with xylene and subjected to gold sputtering.
2.1 The effect of PTFE on the friction and wear performance of PA66
Figure 1 shows the friction and wear properties of PA66/PTFE blends with different PTFE contents (test load was 36 N). As can be seen from Figure 1a, due to the addition of PTFE, the friction test curve of the PA66/PTFE blend shifts downward, indicating that the friction coefficient of the material has been effectively reduced. Moreover, as the PTFE content increases, the reduction in friction coefficient becomes more significant, but the fluctuation amplitude of the friction coefficient also increases. This is likely due to the poor compatibility between PTFE and PA66. The higher the PTFE content, the more defects caused by the poor compatibility between the two phases, leading to an increasingly unstable friction coefficient. As shown in Figure 1b, based on the friction coefficient test curves and the average friction coefficient and volumetric wear rate calculated from the wear height statistics, when the mass fraction of PTFE added is 20%, the friction coefficient of the PA66/F20 material decreases to 0.39, which is a 25.4% reduction compared to pure PA66, providing some degree of self-lubrication improvement. However, due to the poor compatibility between PA66 and PTFE, the volumetric wear rate of the PA66/PTFE blend is higher than that of pure PA66.
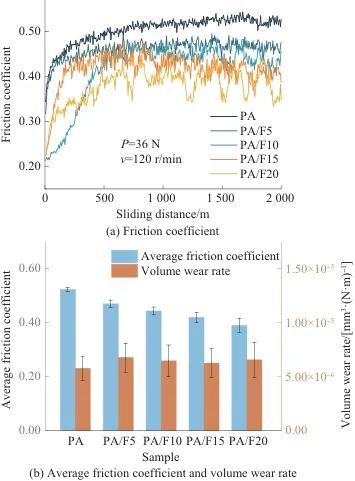
Fig. 1 Friction and wear properties of PA66/PTFE blends filled with different contents of PTFE
2.2 The effect of MAPE on the friction and wear properties of PA66
Figure 2 shows the friction and wear performance tests of PA66/MAPE blend materials filled with different MAPE contents. The data indicate that as the MAPE content increases, the friction coefficient of the PA66/MAPE blend material gradually decreases. When the MAPE mass fraction increases from 5% to 10%, the friction coefficient decreases by 20%. As the MAPE mass fraction increases beyond 10%, the downward trend of the friction coefficient tends to level off.
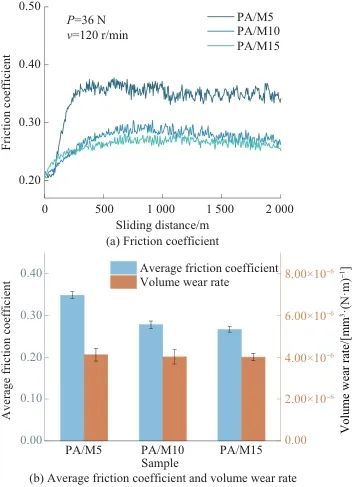
Fig. 2 Friction and wear properties of PA66/MAPE blends filled with different contents of MAPE
2.3 Effect of MAPE on the Properties of PA/PTFE Blends
MAH grafting is used to modify PA66 materials because the introduced MAH groups can form covalent bonds with the amino-H in PA66 through nucleophilic substitution reactions, resulting in good interfacial interactions[30]. With the total mass fraction of PTFE and MAPE fixed at 20%, the friction coefficient curves of PA66/MAPE, PA66/PTFE, and PA66/PTFE/MAPE blends are shown in Fig. 3a, and the average friction coefficients and volume wear rates are presented in Fig. 3b. It is evident that the addition of MAPE significantly reduces the friction coefficients of all samples compared to the sample PA/F20 with only PTFE added, and the friction coefficients are more stable. Among them, the PA/F5/M15 material has the lowest friction coefficient of 0.234, a 55.3% decrease compared to pure PA66's 0.523, and its volume wear rate is 3.23×10^-6 mm³/(N·m), a 44.1% decrease compared to pure PA66's 5.78×10^-6 mm³/(N·m). The average friction coefficient of the PA/F10/M10 material is also only 0.237. The data demonstrate that PTFE and MAPE have a synergistic effect in improving the friction and wear properties of PA66.
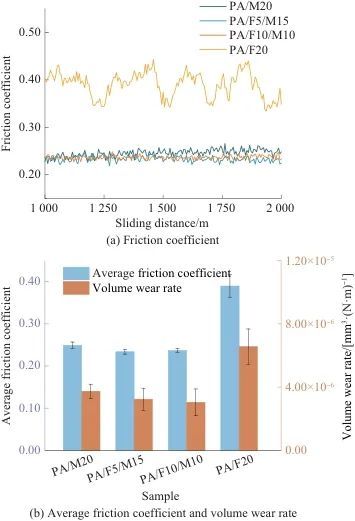
Fig. 3 Friction and wear properties of MAPE-modified PA66/PTFE blend materials
Table 2 presents the bending and tensile properties of PTFE and MAPE modified PA66 blends. As shown in Table 2, both PTFE and MAPE have a negative impact on the mechanical strength and modulus of PA66, with MAPE having a greater influence than PTFE. However, due to the good compatibility between MAPE and PA66, the impact strength of the blend increases with the addition of MAPE. Compared to pure PA66, the impact strength of PA/M20 is approximately 59.3% higher than that of pure PA66 at 8.1 kJ/m². The impact strength of PA/F5/M15 is 103.9% higher than that of PA/F20, which only contains PTFE. The flexural modulus of PA66/PTFE/MAPE shows a certain decrease, indicating a reduction in material rigidity, with the lowest PA/F10/M10 decreasing by only 13.4%.
Table 2 Flexural and tensile properties of PA66/PTFE/MAPE blends
To analyze the mechanism of the effect of MAPE and PTFE on the properties of PA66 blends, SEM was used to conduct morphological analysis of the brittle fracture surfaces of PA/F20, PA/M20, and PA/F10/M10 materials, as shown in Figure 4. In Figure 4b, the fracture surface of PA/F20 is relatively smooth, with clearly visible smooth holes left by the detachment of PTFE, indicating that the compatibility of PTFE with the PA66 matrix is extremely poor, resulting in brittle fracture, and PTFE easily falls off the surface. This should be the reason why the volume wear rate of PA/F20 is greater than that of PA66. In contrast, on the surface of PA/F10/M10, in addition to the dense holes etched by MAPE, there are also many exposed PTFE particles adhering to the surface, indicating that the addition of MAPE has played a role in improving the compatibility between PTFE and the PA66 matrix to some extent.
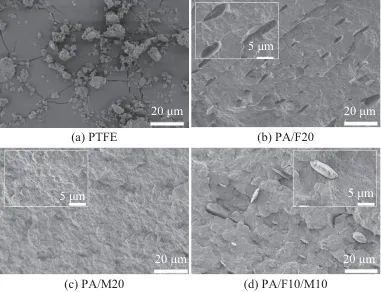
Fig. 4 SEM photos of PTFE and impact fracture surface of PA66/PTFE/MAPE blends
2.4 Long-distance Staged Friction Testing
To further explore the effects of MAPE and PTFE on the friction and wear properties of PA66 materials, long-distance staged friction tests were conducted on each material, as shown in Figure 5. As can be seen from Figure 5, under the same test conditions, the PA/F20 sample with only added PTFE exhibits extremely unstable friction coefficients, with significant fluctuations both between cycles and within cycles. This further indicates poor compatibility between PTFE and the PA66 matrix, and that PTFE tends to peel off during the friction process. The PA/M20 also shows a high friction coefficient during the friction stage when the sliding distance exceeds 2,000 meters. Compared to PA/M20 and PA/F20, PA/F10/M10 demonstrates lower friction coefficients and better stability within the sliding distance range of 0-11,000 meters, indicating the synergistic anti-friction effect of PTFE and MAPE on PA66.
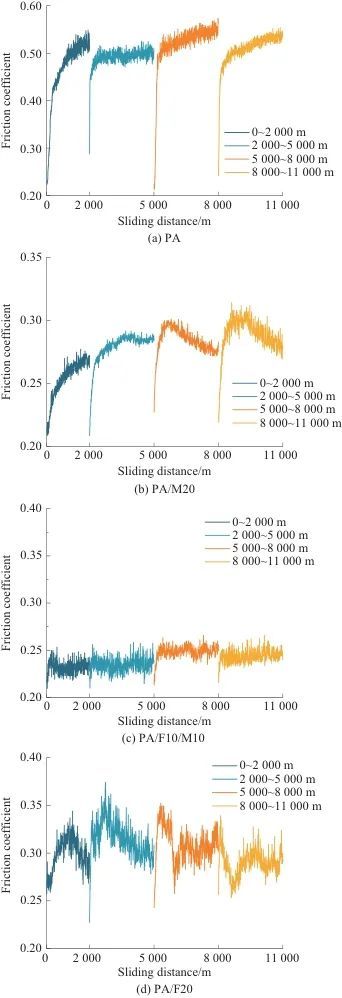
Fig. 5 Friction coefficient of PA66 and its blends at different sliding distances
Figure 6a lists the volumetric wear of PA66 and its blended materials at various stages of the friction test. As shown in Figure 6a, pure PA66 exhibits high volumetric wear at each stage. Notably, for modified materials filled with PTFE or (and) MAPE, as the sliding distance increases regularly, the volumetric wear of the materials gradually decreases, with the reduction rate slowing down and stabilizing at a low level, demonstrating excellent wear resistance. According to the total volumetric wear statistics for the entire cycle (0–11,000 m) in Figure 6b, the PA/F10/M10 material has the lowest total wear, indicating its superior wear resistance.
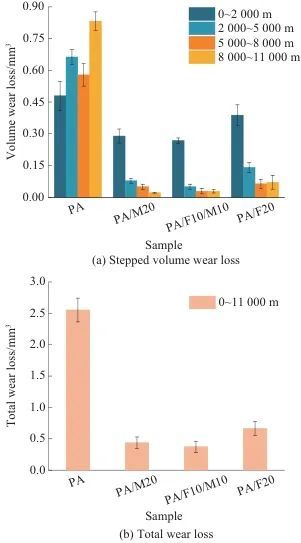
Figure 6 Volume wear loss of PA66 and its composites
In order to better study the friction behavior of PA66 and its blended materials, SEM was used to analyze the wear surface after a sliding distance of 2,000 m, as shown in Figure 7. From Figure 7, it can be observed that the surface of pure PA66 has particle-like substances adhered to it, forming abrasive and adhesive wear marks. The small protruding particles on the surface of PA66 undergo deformation and movement due to shear and frictional heat, with the wear mechanism mainly characterized by abrasive wear and adhesive wear.
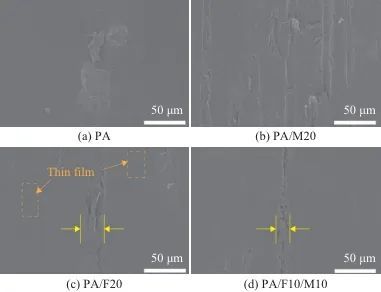
Fig. 7 Morphology of worn surface of PA66 sliding to 2,000 m
MAPE has higher flexibility than PA66. Under friction and shear action, the surface of PA/M20 yields and deforms, forming flake-like wear debris. However, due to its good interfacial interaction with the PA66 matrix, the flake-like wear debris is not easy to detach. As a result, the material exhibits a low friction coefficient and volume wear rate, with the wear mechanism primarily characterized by adhesive wear.
The wear surface of PA/F20 is relatively flat, which is also due to the tendency of PTFE to yield and deform under friction. A careful observation of Figure 7c reveals the presence of some layered material on the surface, which indicates that a discontinuous film layer of PTFE has formed on the friction contact surface, reducing the direct contact between the material and the steel counterpart. This is the main reason for the improved friction coefficient of PA66/PTFE. Due to the weak interaction between PTFE and the matrix, it is prone to fall off from the wear surface, leaving wider wear scars on the surface, which results in extremely unstable friction coefficients and low wear resistance. In contrast, the wear scars along the friction direction on the PA/F10/M10 wear surface are narrower. Analyzing this in conjunction with Figure 4c further demonstrates that MAPE can improve the compatibility of PTFE with the PA66 matrix, enhancing the interaction between PTFE and the PA66 matrix. The PTFE film layer on the friction surface adheres more firmly to the PA66 matrix, resulting in narrower wear scars and improved wear resistance. While enhancing the interaction between PTFE and PA66, MAPE itself also undergoes plastic deformation, promoting the formation of a continuous and uniform transfer film, with the wear mechanism primarily involving adhesive wear.
The effect of MAPE on the friction and wear performance of PA66/PTFE under different loads
At the same test speed (v=120 r/min), friction tests were conducted on PA, PA/M20, PA/F20, and PA/F10/M10 by varying the load (P), and the results are shown in Figure 8. Although the friction coefficient of the PA/F20 material is lower than that of pure PA66 due to the self-lubricating properties of PTFE, the friction coefficient exhibits significant fluctuations because PTFE is prone to detachment, and the test process is accompanied by substantial vibration noise.
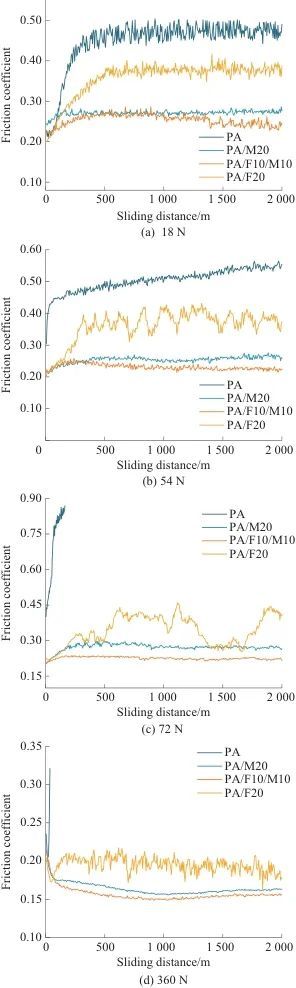
Fig. 8 Friction coefficient of PA66 and its composites under different loads
With the addition of MAPE, the corresponding materials exhibit lower friction coefficients under both low and high loads. Among them, the PA/F10/M10 material demonstrates a good synergistic improvement effect, showing the lowest and most stable friction coefficient.
Table 3 shows the volume wear rates of various PA66 samples under different test loads. As can be seen from Table 3, the volume wear rates of PA/F10/M10 are lower than those of PA/F20 and PA/M20 under different loads, which further indicates that MAPE and PTFE have a friction-reducing effect on PA66, and the wear resistance of PA66 material is further improved.
Tab. 3 Volume wear rate of PA, PA/M20, PA/F20, PA/F10/M10 under different loads mm3/(N·m)
3 Conclusion
The PA66-based blend material (PA/PTFE/MAPE) modified by PTFE and MAPE was prepared using the melt blending method, and friction and wear tests were conducted under dry friction conditions. SEM was used to analyze the surface morphology of the material cross-section and wear surface, and the friction and wear mechanism was discussed. The following conclusions were drawn:
(1) The addition of PTFE can reduce the friction coefficient of PA66 to some extent. However, due to its poor compatibility with PA66, PTFE tends to detach during friction, resulting in a high volume wear rate and unstable friction coefficient for the PA66/PTFE material.
MAPE can significantly improve the friction and wear performance of PA66/PTFE materials. Under different friction test conditions, MAPE and PTFE have a synergistic effect on the friction and wear performance of PA66, while the total filling amount of PTFE and MAPE (mass fraction 20%) remains unchanged. The materials exhibit a low and stable friction coefficient and a low volume wear rate. In the friction test with a load of 54 N, the average friction coefficient and volume wear rate of PA/F10/M10 materials are 0.237 and 1.7×10^-6 mm³/(N∙m), respectively.
(3) SEM analysis shows that MAPE has good compatibility with PTFE, which can improve the interfacial interaction between PA66 and PTFE, thus enhancing the impact toughness and friction-wear properties of the material.
【Copyright and Disclaimer】The above information is collected and organized by PlastMatch. The copyright belongs to the original author. This article is reprinted for the purpose of providing more information, and it does not imply that PlastMatch endorses the views expressed in the article or guarantees its accuracy. If there are any errors in the source attribution or if your legitimate rights have been infringed, please contact us, and we will promptly correct or remove the content. If other media, websites, or individuals use the aforementioned content, they must clearly indicate the original source and origin of the work and assume legal responsibility on their own.