In which fields is medical PC used?
In the medical field, plastic products must meet specific standards of chemical stability and biological safety due to their potential contact with medications or the human body.
In short, medical plastics should not release harmful substances during use, avoiding toxicity or injury to tissues and organs, and maintaining harmlessness to the human body.
To ensure the biological safety of medical plastics, all medical plastic products sold on the market need to undergo strict certification and testing by authoritative institutions in the healthcare industry. Additionally, it is necessary to clearly indicate to users which specific plastic models are designed for medical purposes, i.e., medical-grade plastics.
Medical devices come in a wide variety, including in vitro diagnostic reagents, medical consumables, medical equipment, and pharmaceutical equipment. Due to the advantages of low cost, ease of processing, light weight, and good toughness, plastics are increasingly being used in medical devices.
01
Polycarbonate PC
Polycarbonate (PC) is a general term for a class of high molecular polymers containing carbonate groups in their molecular chains. Depending on the type of ester group, they can be divided into aliphatic PCs, alicyclic PCs, and aromatic PCs, etc.
PC is a thermoplastic engineering plastic with excellent transparency, impact resistance, heat resistance, and mechanical strength.
The synthesis of PC usually involves two processes: phosgene method and non-phosgene method.
Phosgene method: This includes solution phosgenation, interfacial polycondensation, and transesterification. Interfacial polycondensation is currently the most commonly used method, involving the reaction between bisphenol A sodium salt and phosgene to produce polycarbonate. This method is mature, stable in production, and easy to control.
Non-phosgene method: This mainly involves the transesterification reaction between dimethyl carbonate and phenol to produce diphenyl carbonate, followed by transesterification and polycondensation reactions with bisphenol A to generate polycarbonate. This method is referred to as a "green process" because it does not use toxic phosgene as a raw material, making it safer for the environment and operators.
02
In the medical field, plastic products must meet specific standards of chemical stability and biological safety due to their potential contact with drugs or the human body.
In short, medical plastics should not release harmful substances during use, avoiding toxicity or damage to tissues and organs, and maintaining harmlessness to the human body.
To ensure the biological safety of medical plastics, all medical plastic products sold on the market must undergo strict certification and testing by authoritative institutions in the medical industry. In addition, it is necessary to clearly indicate to users which specific plastic models are designed for medical purposes, i.e., medical-grade plastics.
Medical devices come in a wide variety, including in vitro diagnostic reagents, medical consumables, medical equipment, and pharmaceutical equipment. Due to the advantages of low cost, ease of processing, light weight, and good toughness, plastics are increasingly being used in medical devices.
01
Polycarbonate PC
Polycarbonate (PC) is a general term for a class of high molecular polymers containing carbonate groups. Depending on the type of ester group, they can be classified as aliphatic PC, alicyclic PC, and aromatic PC, etc.
PC is a thermoplastic engineering plastic with excellent transparency, impact resistance, heat resistance, and mechanical strength.
The synthesis of PC typically involves two processes: phosgene method and non-phosgene method.
Phosgene method: This includes solution phosgenation, interfacial polycondensation, and transesterification. Interfacial polycondensation is currently the most commonly used method, involving the reaction between sodium salt of bisphenol A and phosgene to produce polycarbonate. This method is mature, stable in production, and easy to control.
Non-phosgene method: This mainly involves the transesterification reaction between dimethyl carbonate and phenol to produce diphenyl carbonate, which then undergoes transesterification and polycondensation reactions with bisphenol A to produce polycarbonate. This method is known as a "green process" because it does not use toxic phosgene as a raw material, making it safer for the environment and operators.
02
In the medical field, plastic products must meet specific standards of chemical stability and biological safety due to their potential contact with drugs or the human body.
In short, medical plastics should not release harmful substances during use, avoiding toxicity or damage to tissues and organs, and maintaining harmlessness to the human body.
To ensure the biological safety of medical plastics, all medical plastic products sold on the market must undergo strict certification and testing by authoritative institutions in the medical industry. In addition, it is necessary to clearly indicate to users which specific plastic models are designed for medical purposes, i.e., medical-grade plastics.
Medical devices come in a wide variety, including in vitro diagnostic reagents, medical consumables, medical equipment, and pharmaceutical equipment. Due to the advantages of low cost, ease of processing, light weight, and good toughness, plastics are increasingly widely used in medical devices.
01
Polycarbonate PC
01
Polycarbonate PC
01
Polycarbonate PC
01
01
01
01
01
01
0101Polycarbonate PC
Polycarbonate PC
Polycarbonate PC
Polycarbonate PC
Polycarbonate PCPolycarbonate PCPolycarbonate (PC) is a general term for a class of high molecular weight polymers that contain carbonate groups in their molecular chains. Depending on the type of ester group, they can be classified as aliphatic PC, alicyclic PC, and aromatic PC, etc.
Polycarbonate (PC) is a general term for a class of high molecular weight polymers that contain carbonate groups in their molecular chains. Depending on the type of ester group, they can be classified as aliphatic PC, alicyclic PC, and aromatic PC, etc.PC is a thermoplastic engineering plastic with excellent transparency, impact resistance, heat resistance, and mechanical strength.
The synthesis of PC typically involves two processes: the phosgene process and the non-phosgene process.
Phosgene process: This includes solution phosgenation, interfacial polycondensation, and transesterification. Interfacial polycondensation is currently the most commonly used method, which involves the reaction between sodium salt of bisphenol A and phosgene to produce polycarbonate. This method is mature, stable in production, and easy to control.
Non-phosgene process: This mainly involves the ester exchange reaction between dimethyl carbonate and phenol to produce diphenyl carbonate, followed by an ester exchange and polycondensation reaction with bisphenol A to form polycarbonate. This method is known as a "green process" because it does not use toxic phosgene as a raw material, making it safer for the environment and operators.
Phosgene process: This includes solution phosgenation, interfacial polycondensation, and transesterification. Interfacial polycondensation is currently the most commonly used method, which involves the reaction between sodium salt of bisphenol A and phosgene to produce polycarbonate. This method is mature, stable in production, and easy to control.
Non-phosgene process: This mainly involves the ester exchange reaction between dimethyl carbonate and phenol to produce diphenyl carbonate, followed by an ester exchange and polycondensation reaction with bisphenol A to form polycarbonate. This method is known as a "green process" because it does not use toxic phosgene as a raw material, making it safer for the environment and operators.
Phosgene process: This includes solution phosgenation, interfacial polycondensation, and transesterification. Interfacial polycondensation is currently the most commonly used method, which involves the reaction between sodium salt of bisphenol A and phosgene to produce polycarbonate. This method is mature, stable in production, and easy to control.
Phosgene process: This includes solution phosgenation, interfacial polycondensation, and transesterification. Interfacial polycondensation is currently the most commonly used method, which involves the reaction between sodium salt of bisphenol A and phosgene to produce polycarbonate. This method is mature, stable in production, and easy to control.
Non-phosgene process: This mainly involves the ester exchange reaction between dimethyl carbonate and phenol to produce diphenyl carbonate, followed by an ester exchange and polycondensation reaction with bisphenol A to form polycarbonate. This method is known as a "green process" because it does not use toxic phosgene as a raw material, making it safer for the environment and operators.
Non-phosgene process: This mainly involves the ester exchange reaction between dimethyl carbonate and phenol to produce diphenyl carbonate, followed by an ester exchange and polycondensation reaction with bisphenol A to form polycarbonate. This method is known as a "green process" because it does not use toxic phosgene as a raw material, making it safer for the environment and operators.
Non-phosgene method: This mainly involves the ester exchange reaction between dimethyl carbonate and phenol to produce diphenyl carbonate, which then undergoes ester exchange and condensation reactions with bisphenol A to generate polycarbonate. This method is referred to as a "green process" because it does not use toxic phosgene as a raw material, making it safer for the environment and operators.
02
Medical-grade PC
02
Medical-grade PC
02
Medical-grade PC
02
02
02
02
02
02
0202Medical-grade PC
Medical-grade PC
Medical-grade PC
Medical-grade PC
Medical-grade PCMedical-grade PCChina started relatively late in the field of medical plastic products, beginning to research and produce plastic infusion bags only in the 1970s.
China started relatively late in the field of medical plastic products, beginning to research and produce plastic infusion bags only in the 1970s.In 1987, the Ministry of Health issued a notice on promoting the use of disposable plastic infusion sets, blood transfusion sets, and syringes. The implementation of this policy greatly promoted the development and production of medical plastic products in China, while also improving the safety and convenience of medical supplies, thus driving the rapid development of related industries.
In 1987, the Ministry of Health issued a notice on promoting the use of disposable plastic infusion sets, blood transfusion sets, and syringes. The implementation of this policy greatly promoted the development and production of medical plastic products in China, while also improving the safety and convenience of medical supplies, thus driving the rapid development of related industries.In the field of medical devices, there is a series of specific performance requirements for the polymer materials used to ensure their safety and effectiveness. Common requirements are as follows:
Chemical stability: The material should have excellent chemical resistance, ensuring that it maintains its properties throughout the expected usage period, even during routine disinfection processes without being damaged.
Processability: The material should be easy to process, facilitating the manufacture of various complex-shaped medical products.
Biological safety: It must be non-toxic, free from risks of causing cancer, teratogenic effects, or genetic mutations, not induce pyrogenic reactions, and the content of leachables and extractables should be controlled at extremely low levels.
Tissue compatibility: The material should not damage surrounding tissues, interfere with the body's immune response, or lead to calcification on the surface of the material.
Blood compatibility: When in contact with blood, the material should exhibit good anticoagulant properties, avoiding hemolysis, reduction in the number of blood cells, denaturation of proteins in the blood, or destruction of formed elements in the blood.
Long-term stability: After implantation in the human body, the material should demonstrate good stability, and its mechanical properties should remain stable over long-term use, without significant changes (for non-degradable materials).
These requirements ensure that the application of polymer materials in medical devices is not only safe and effective but also meets the needs of long-term clinical use.
In the field of medical devices, there are a series of specific performance requirements for the high molecular materials used to ensure their safety and effectiveness. The common requirements are as follows:
Chemical stability: It should have excellent chemical resistance, ensuring that its performance is maintained over the expected service life, even during routine disinfection processes without being damaged.
Processability: The material should be easy to process, making it convenient to manufacture into various complex shapes of medical products.
Biological safety: It must be non-toxic, with no risk of causing cancer, teratogenicity, or genetic mutations, not causing pyrogenic reactions, and the content of leachables and extractables should be controlled at very low levels.
Tissue compatibility: The material should not damage surrounding tissues, not interfere with the human immune response, and not cause calcification on the surface of the material.
Blood compatibility: When the material comes into contact with blood, it should have good anticoagulant properties, avoiding hemolysis, reduction in blood cell count, denaturation or destruction of proteins in the blood, or other formed elements in the blood.
Long-term stability: After implantation in the human body, the material should exhibit good stability, and its mechanical properties should remain stable over long-term use, without significant changes (for non-degradable materials).
These requirements ensure that the application of high molecular materials in medical devices is not only safe and effective but also meets the needs of long-term clinical use.
In the field of medical devices, there are a series of specific performance requirements for the high molecular materials used to ensure their safety and effectiveness. The common requirements are as follows:
In the field of medical devices, there are a series of specific performance requirements for the high molecular materials used to ensure their safety and effectiveness. The common requirements are as follows:
In the field of medical devices, there are a series of specific performance requirements for the high molecular materials used to ensure their safety and effectiveness. The common requirements are as follows:Chemical stability: It should have excellent chemical resistance, ensuring that its performance is maintained over the expected service life, even during routine disinfection processes without being damaged.
Chemical stability: It should have excellent chemical resistance, ensuring that its performance is maintained over the expected service life, even during routine disinfection processes without being damaged.
Chemical stability: It should have excellent chemical resistance, ensuring that its performance is maintained over the expected service life, even during routine disinfection processes without being damaged.Processability: The material should be easy to process, making it convenient to manufacture into various complex shapes of medical products.
Processability: The material should be easy to process, making it convenient to manufacture into various complex shapes of medical products.
Processability: The material should be easy to process, making it convenient to manufacture into various complex shapes of medical products.Biological safety: Must be non-toxic, without the risk of causing cancer, teratogenicity, or genetic mutations, and should not cause pyrogenic reactions. The content of leachables and extractables should be controlled at an extremely low level.
Biological safety: Must be non-toxic, without the risk of causing cancer, teratogenicity, or genetic mutations, and should not cause pyrogenic reactions. The content of leachables and extractables should be controlled at an extremely low level.
Biological safety: Must be non-toxic, without the risk of causing cancer, teratogenicity, or genetic mutations, and should not cause pyrogenic reactions. The content of leachables and extractables should be controlled at an extremely low level.Tissue compatibility: The material should not damage surrounding tissues, interfere with the body's immune response, or lead to calcification on the material surface.
Tissue compatibility: The material should not damage surrounding tissues, interfere with the body's immune response, or lead to calcification on the material surface.
Tissue compatibility: The material should not damage surrounding tissues, interfere with the body's immune response, or lead to calcification on the material surface.Blood compatibility: When in contact with blood, the material should have good anticoagulant properties, avoiding hemolysis, reduction in blood cell count, denaturation of proteins in the blood, or destruction of formed elements in the blood.
Blood compatibility: When in contact with blood, the material should have good anticoagulant properties, avoiding hemolysis, reduction in blood cell count, denaturation of proteins in the blood, or destruction of formed elements in the blood.
Blood compatibility: When in contact with blood, the material should have good anticoagulant properties, avoiding hemolysis, reduction in blood cell count, denaturation of proteins in the blood, or destruction of formed elements in the blood.Long-term stability: After being implanted in the human body, the material should exhibit good stability, and its mechanical properties should remain stable over long-term use, without significant changes (for non-degradable materials).
Long-term stability: After being implanted in the human body, the material should exhibit good stability, and its mechanical properties should remain stable over long-term use, without significant changes (for non-degradable materials).
Long-term stability: After being implanted in the human body, the material should exhibit good stability, and its mechanical properties should remain stable over long-term use, without significant changes (for non-degradable materials).These requirements ensure that polymer materials used in medical devices are not only safe and effective but also meet the needs for long-term clinical use.
These requirements ensure that polymer materials used in medical devices are not only safe and effective but also meet the needs for long-term clinical use.
These requirements ensure that polymer materials used in medical devices are not only safe and effective but also meet the needs for long-term clinical use.Currently, medical plastics mainly include engineering plastics and biodegradable materials, as well as some special materials such as silicone. There are many types of medical plastics, approximately a dozen, among which the market share of medical-grade polycarbonate (PC) is continuously increasing.
Currently, medical plastics mainly include engineering plastics and biodegradable materials, as well as some special materials such as silicone. There are many types of medical plastics, approximately a dozen, among which the market share of medical-grade polycarbonate (PC) is continuously increasing.Polycarbonate (PC) is widely used in the medical industry due to its unique material properties.
Polycarbonate (PC) is widely used in the medical industry due to its unique material properties.Transparency: PC has extremely high transparency, which is very important for medical devices that require optical clarity.
Impact resistance: PC has excellent impact resistance and can maintain its physical properties even at low temperatures, making it suitable for applications that require withstanding impacts.
Heat resistance: PC has a relatively high glass transition temperature (Tg), allowing it to be used over a wide temperature range, which is suitable for medical equipment requiring high-temperature sterilization.
Chemical resistance: PC shows good resistance to most inorganic acids, alkalis, and salts, making it suitable for use during chemical disinfection processes.
Biocompatibility: PC has good biocompatibility and can be compatible with human tissues, making it suitable for implantable medical devices.
Processability: PC is easy to process and can be shaped through injection molding, extrusion, and other methods. Its adaptability makes it suitable for manufacturing complex components of medical equipment.
Environmental stability: PC has good resistance to water, oil, and many chemicals, making it suitable for use in various medical environments.
Transparency: PC has extremely high transparency, which is very important for medical devices that require optical clarity.
Impact resistance: PC has excellent impact resistance and can maintain its physical properties even at low temperatures, making it suitable for applications that require withstanding impacts.
Heat resistance: PC has a relatively high glass transition temperature (Tg), allowing it to be used over a wide temperature range, which is suitable for medical equipment requiring high-temperature sterilization.
Chemical resistance: PC shows good resistance to most inorganic acids, alkalis, and salts, making it suitable for use during chemical disinfection processes.
Biocompatibility: PC has good biocompatibility and can be compatible with human tissues, making it suitable for implantable medical devices.
Processability: PC is easy to process and can be shaped through injection molding, extrusion, and other methods. Its adaptability makes it suitable for manufacturing complex components of medical equipment.
Environmental stability: PC has good resistance to water, oil, and many chemicals, making it suitable for use in various medical environments.
Transparency: PC has extremely high transparency, which is very important for medical devices that require optical clarity.
Transparency: PC has extremely high transparency, which is very important for medical devices that require optical clarity.
Transparency: PC has extremely high transparency, which is very important for medical devices that require optical clarity.Impact resistance: PC has excellent impact resistance and can maintain its physical properties even at low temperatures, making it suitable for applications that require withstanding impacts.
Impact resistance: PC has excellent impact resistance and can maintain its physical properties even at low temperatures, making it suitable for applications that require withstanding impacts.
Impact resistance: PC has excellent impact resistance and can maintain its physical properties even at low temperatures, making it suitable for applications that require withstanding impacts.Heat resistance: PC has a high glass transition temperature (Tg) and can be used over a wide temperature range, making it suitable for medical devices that require high-temperature sterilization.
Heat resistance: PC has a high glass transition temperature (Tg) and can be used over a wide temperature range, making it suitable for medical devices that require high-temperature sterilization.
Heat resistance: PC has a high glass transition temperature (Tg) and can be used over a wide temperature range, making it suitable for medical devices that require high-temperature sterilization.Chemical resistance: PC has good resistance to most inorganic acids, bases, and salts, making it suitable for use in chemical disinfection processes.
Chemical resistance: PC has good resistance to most inorganic acids, bases, and salts, making it suitable for use in chemical disinfection processes.
Chemical resistance: PC has good resistance to most inorganic acids, bases, and salts, making it suitable for use in chemical disinfection processes.Biocompatibility: PC has good biocompatibility and can be compatible with human tissues, making it suitable for implantable medical devices.
Biocompatibility: PC has good biocompatibility and can be compatible with human tissues, making it suitable for implantable medical devices.
Biocompatibility: PC has good biocompatibility and can be compatible with human tissues, making it suitable for implantable medical devices.Processability: PC is easy to process and can be formed through injection molding, extrusion, and other methods, offering strong adaptability and suitability for manufacturing complex medical device components.
Processability: PC is easy to process and can be formed through injection molding, extrusion, and other methods, offering strong adaptability and suitability for manufacturing complex medical device components.
Processability: PC is easy to process and can be formed through injection molding, extrusion, and other methods, offering strong adaptability and suitability for manufacturing complex medical device components.Environmental stability: PC has good resistance to water, oil, and many chemicals, making it suitable for use in various medical environments.
Environmental stability: PC has good resistance to water, oil, and many chemicals, making it suitable for use in various medical environments.
Environmental stability: PC has good resistance to water, oil, and many chemicals, making it suitable for use in various medical environments.Due to the extremely high requirements for material safety and reliability in the medical industry, these characteristics of polycarbonate make it an indispensable material in the medical field.
Due to the extremely high requirements for material safety and reliability in the medical industry, these characteristics of polycarbonate make it an indispensable material in the medical field.However, it should also be noted that under certain conditions, polycarbonate may release bisphenol A (BPA), thus its use in some applications, such as baby bottles and certain medical devices, has been restricted and scrutinized.
However, it should also be noted that under certain conditions, polycarbonate may release bisphenol A (BPA), thus its use in some applications, such as baby bottles and certain medical devices, has been restricted and scrutinized.
03
Medical-grade PC Applications
03
Medical-grade PC Applications
03
Medical-grade PC Applications
03
03
03
03
03
03
0303Medical-grade PC Applications
Medical-grade PC Applications
Medical-grade PC Applications
Medical-grade PC Applications
Medical-grade PC ApplicationsMedical-grade PC ApplicationsMedical Devices: Due to its heat resistance, chemical resistance, and transparency, PC is used in the manufacturing of medical devices such as syringes, dialyzers, and surgical instruments.
Diagnostic Equipment: Polycarbonate is used to manufacture transparent parts of some diagnostic equipment, such as lenses and cover glasses for optical microscopes.
Artificial Organs: The biocompatibility of PC makes it one of the ideal materials for artificial organs (such as heart valves and artificial blood vessels).
Drug Delivery Systems: Polycarbonate is used in the design and manufacture of drug delivery systems, such as capsules and implants for controlled-release drugs.
Housings and Protective Covers for Medical Equipment: The impact resistance and transparency of PC make it suitable for manufacturing housings and protective covers for medical equipment.
Medical Devices: Due to its heat resistance, chemical resistance, and transparency, PC is used in the manufacturing of medical devices such as syringes, dialyzers, and surgical instruments.
Diagnostic Equipment: Polycarbonate is used for making transparent parts of some diagnostic equipment, such as lenses and cover glasses for optical microscopes.
Artificial Organs: The biocompatibility of PC makes it one of the ideal materials for artificial organs (such as heart valves, artificial blood vessels).
Drug Delivery Systems: Polycarbonate is used in the design and manufacture of drug delivery systems, such as capsules and implants for controlled-release drugs.
Housings and Protective Covers for Medical Equipment: The impact resistance and transparency of PC make it suitable for manufacturing housings and protective covers for medical equipment.
Medical Devices: Due to its heat resistance, chemical resistance, and transparency, PC is used in the manufacturing of medical devices such as syringes, dialyzers, and surgical instruments.
Medical Devices: Due to its heat resistance, chemical resistance, and transparency, PC is used in the manufacturing of medical devices such as syringes, dialyzers, and surgical instruments.
Medical Devices: Due to its heat resistance, chemical resistance, and transparency, PC is used in the manufacturing of medical devices such as syringes, dialyzers, and surgical instruments.Diagnostic Equipment: Polycarbonate is used for making transparent parts of some diagnostic equipment, such as lenses and cover glasses for optical microscopes.
Diagnostic Equipment: Polycarbonate is used for making transparent parts of some diagnostic equipment, such as lenses and cover glasses for optical microscopes.
Diagnostic Equipment: Polycarbonate is used for making transparent parts of some diagnostic equipment, such as lenses and cover glasses for optical microscopes.Artificial Organs: The biocompatibility of PC makes it one of the ideal materials for artificial organs (such as heart valves, artificial blood vessels).
Artificial Organs: The biocompatibility of PC makes it one of the ideal materials for artificial organs (such as heart valves, artificial blood vessels).
Artificial Organs: The biocompatibility of PC makes it one of the ideal materials for artificial organs (such as heart valves, artificial blood vessels).Drug Delivery Systems: Polycarbonate is used in the design and manufacture of drug delivery systems, such as capsules and implants for controlled-release drugs.
Drug Delivery Systems: Polycarbonate is used in the design and manufacture of drug delivery systems, such as capsules and implants for controlled-release drugs.
Drug Delivery Systems: Polycarbonate is used in the design and manufacture of drug delivery systems, such as capsules and implants for controlled-release drugs.Housings and Protective Covers for Medical Equipment: The impact resistance and transparency of PC make it suitable for manufacturing housings and protective covers for medical equipment.
Housings and Protective Covers for Medical Equipment: The impact resistance and transparency of PC make it suitable for manufacturing housings and protective covers for medical equipment.
Housings and Protective Covers for Medical Equipment: The impact resistance and transparency of PC make it suitable for manufacturing housings and protective covers for medical equipment.
04
Teijin | Medical Grade PC
04
Teijin | Medical Grade PC
04
Teijin | Medical Grade PC
04
04
04
04
04
04
0404Teijin | Medical Grade PC
Teijin | Medical Grade PC
Teijin | Medical Grade PC
Teijin | Medical Grade PC
Teijin | Medical Grade PCTeijin | Medical Grade PCTeijin's medical-grade transparent PC, while maintaining the transparency and impact resistance of general PCs, is a series of products that also endow materials with properties such as resistance to gamma rays, electron beam sterilization, and steam sterilization. This makes it suitable for various medical device applications.
Teijin's medical-grade transparent PC, while maintaining the transparency and impact resistance of general PCs, is a series of products that also endow materials with properties such as resistance to gamma rays, electron beam sterilization, and steam sterilization. This makes it suitable for various medical device applications.Features
Biocompatible materials have passed the biocompatibility tests according to ISO10993.
A variety of products with different flowabilities are available.
Features
Biocompatible materials have passed the biocompatibility tests according to ISO10993.
A variety of products with different flowabilities are available.
Features
Features
Features
FeaturesBiocompatible materials have passed the biocompatibility test of ISO10993.
Biocompatible materials have passed the biocompatibility test of ISO10993.
Biocompatible materials have passed the biocompatibility test of ISO10993.
Biocompatible materials have passed the biocompatibility test of ISO10993.A variety of products with different fluidities are available for selection.
A variety of products with different fluidities are available for selection.
A variety of products with different fluidities are available for selection.
A variety of products with different fluidities are available for selection.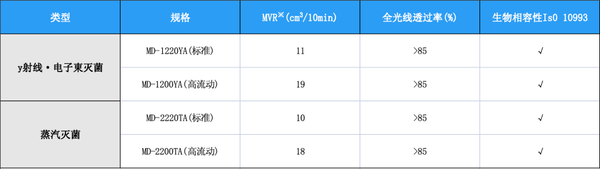
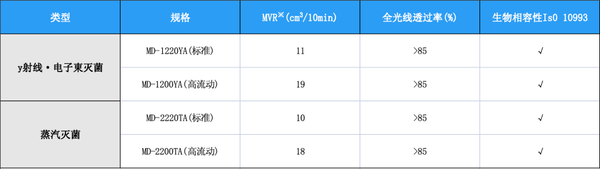
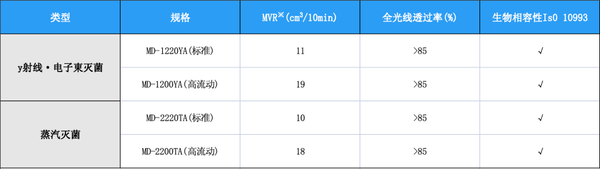
Gamma Ray and Electron Beam Sterilization Specifications
Gamma Ray and Electron Beam Sterilization Specifications
Gamma Ray and Electron Beam Sterilization Specifications
Gamma Ray and Electron Beam Sterilization Specifications
Gamma Ray and Electron Beam Sterilization SpecificationsThe MD-12 series. Compared to general PC and similar products on the market, after treatment with γ-rays and electron beams, the MD-12 series exhibits minimal color phase changes, maintaining good color stability, making it suitable for use in applications requiring γ-ray and electron beam sterilization.
The MD-12 series. Compared to general PC and similar products on the market, after treatment with γ-rays and electron beams, the MD-12 series exhibits minimal color phase changes, maintaining good color stability, making it suitable for use in applications requiring γ-ray and electron beam sterilization.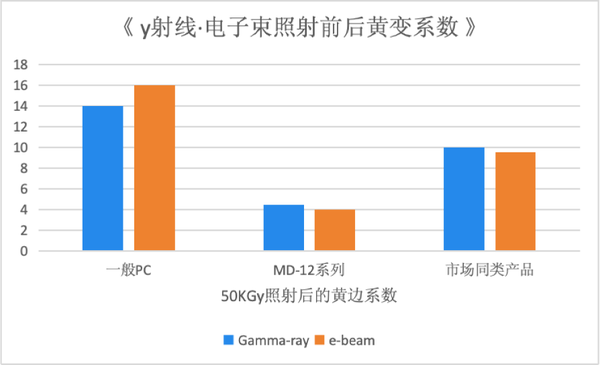
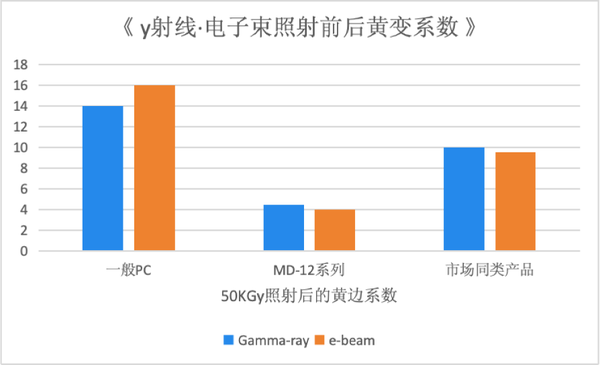
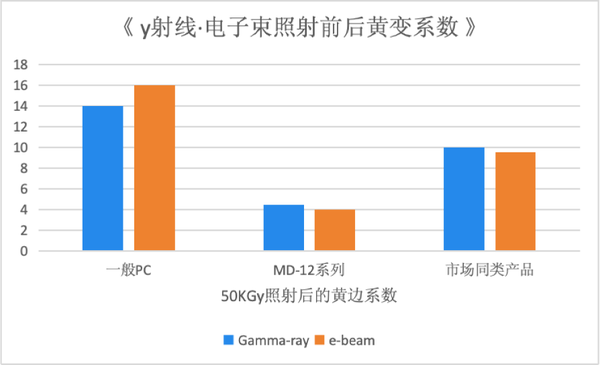
Steam Sterilization Specifications
Steam sterilization resistance specifications
Steam sterilization resistance specifications
Steam sterilization resistance specifications
Steam sterilization resistance specificationsMD-22 Series. Compared to the existing competitive steam resistance specifications, the MD-22 series can maintain good transparency after steam treatment.
MD-22 Series. Compared to the existing competitive steam resistance specifications, the MD-22 series can maintain good transparency after steam treatment.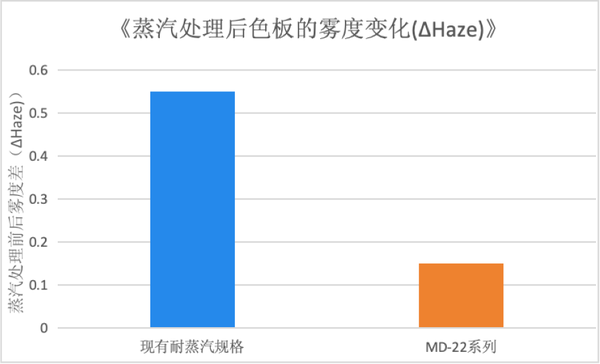
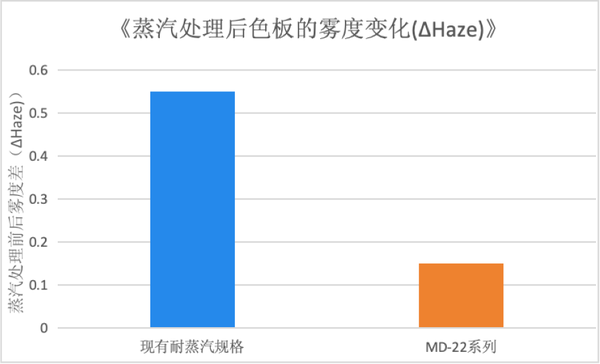
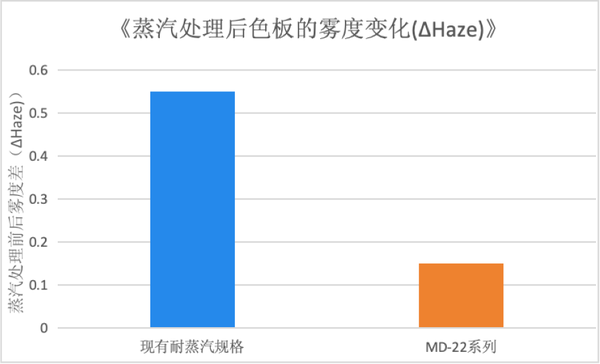
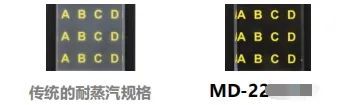
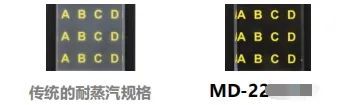
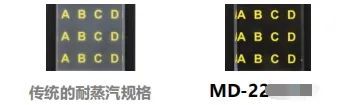
Fat-resistant emulsion specification
Fat-resistant emulsion specification
Fat-resistant emulsion specification
Fat-resistant emulsion specification
Fat-resistant emulsion specificationCompared to general PC, the MD-12 series has "suppression of color changes caused by v-rays and electron beam irradiation" and "extremely high resistance to fat emulsions," making it very suitable for medical consumables (especially in areas prone to stress)
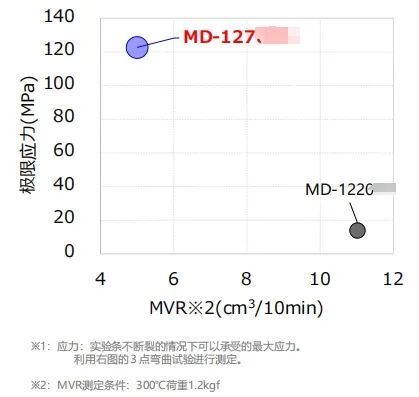
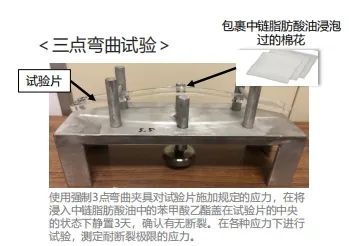
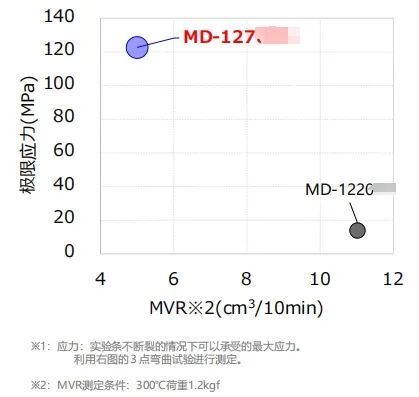
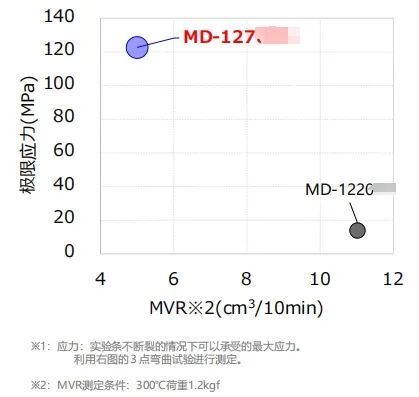
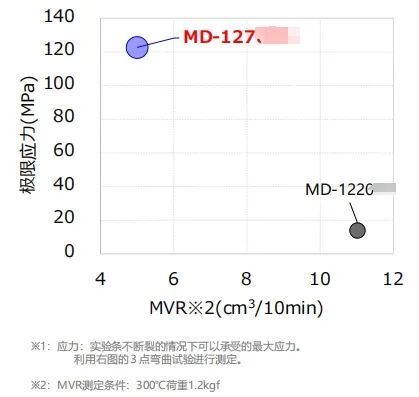
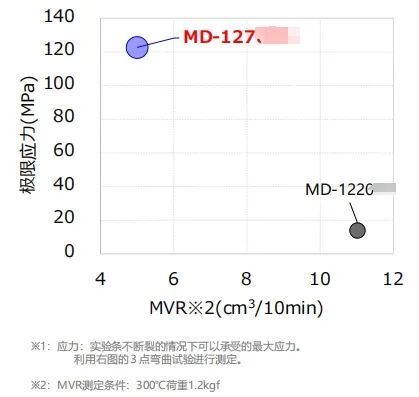
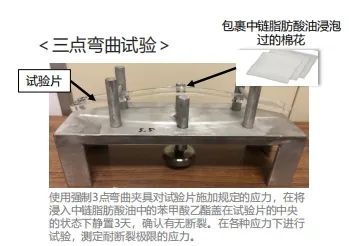
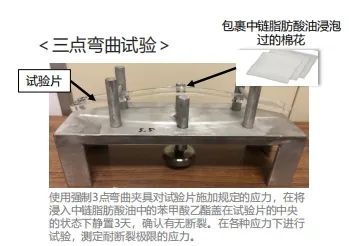
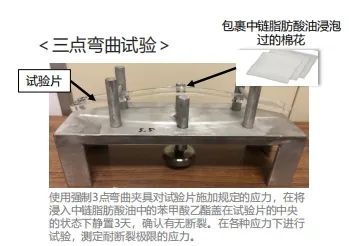
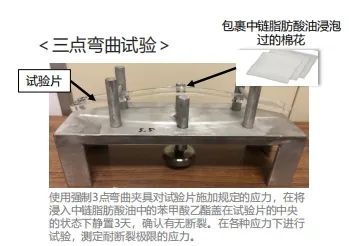
【Copyright and Disclaimer】The above information is collected and organized by PlastMatch. The copyright belongs to the original author. This article is reprinted for the purpose of providing more information, and it does not imply that PlastMatch endorses the views expressed in the article or guarantees its accuracy. If there are any errors in the source attribution or if your legitimate rights have been infringed, please contact us, and we will promptly correct or remove the content. If other media, websites, or individuals use the aforementioned content, they must clearly indicate the original source and origin of the work and assume legal responsibility on their own.
Most Popular
-
Four Major Chemical New Material Giants Sell Off and Shut Down Again!
-
Covestro faces force majeure!
-
DuPont to Spin Off Nomex and Kevlar Brands for $14.4 Billion: Is Aramid Fiber Still Attractive?
-
Massive Retreat of Japanese and Korean Battery Manufacturers
-
Napan Unveils Thermoplastic Composite Three-in-One Power System Solution, Battery Cover Weight Reduced by 67%