Leading enterprise invests 10 billion yuan! Regenerated fiber capacity may exceed 20 million tons by 2025!
On one side, there are enterprises investing billions and projects flourishing everywhere; on the other side, there are concerns about overcapacity and the market's ability to absorb it. Driven by environmental policies and market demand, recycled fiber projects are advancing at breakneck speed, yet underlying issues are quietly brewing.
As a crucial component in driving the green and circular economy, the recycled fiber market has experienced unprecedented development opportunities in recent years. Textile companies supplying major brands like Adidas, Inditex, H&M, and Uniqlo have felt this shift particularly keenly. Brands are increasingly demanding that suppliers provide more environmentally friendly fibers, with the annual usage of recycled fibers gradually increasing. Additionally, fabric exporters to the EU, affected by the ESPR set to take effect on July 18, 2024, face even higher requirements for the green and sustainable attributes of their fabrics.
As a result, more and more upstream companies are making significant investments in related fields, among which leading enterprises have invested billions.
Peipu Launches FixDye Eco-Friendly Recycled Polyester Filament
The production capacity will reach 250,000 tons.
On March 12, "Regeneration Recycles, Greening the Future — FixDye Eco-friendly Recycled Polyester Fiber Press Conference" was held at the National Exhibition and Convention Center (Shanghai). At the conference, PEPO Technology Group (REO-ECO) released the FixDye eco-friendly recycled polyester fiber.
FixDye eco-friendly recycled polyester filament uses raw materials such as plastic bottles, waste yarn, and fabric scraps. Combined with 100% imported equipment from巴马格 (Barmag) and TMT, it employs advanced direct spinning technology to significantly shorten the production process while enhancing product quality. The recycled polyester filament includes high-quality yarns like POY, FDY, and DTY, which are widely used in apparel, home textiles, and other fields, meeting the market demand for high-quality recycled fibers.
As an environmental technology company specializing in the recycling of polymer materials, Peipu boasts a 100% vertically integrated full-industry-chain factory, with an annual production capacity of 250,000 tons of recycled polyester filament. It focuses solely on the production of recycled products, ensuring the authenticity and traceability of its products. Meanwhile, Peipu actively adopts clean energy sources such as photovoltaic and wind power, striving to build a green factory and contribute to environmental protection. Currently, its ColorSpun project will realize the full-industry-chain production from waste bottles to recycled polyester colored filament (FixDye), with the first phase of spinning capacity reaching 100,000 tons and the total capacity reaching 250,000 tons.
Huai'an City's Annual Production of 500,000 Tons of Recycled Polyester New Material Project
Jiangsu Lusikela New Materials Co., Ltd.'s 500,000-ton recycled polyester new material project has a total investment of 5 billion yuan. It will build a 500,000-ton/year engineering project for regenerating polyester new materials from waste polyester textile products, carried out in two phases. In phase one, an investment of 1.1 billion yuan is planned, with the purchase of 118,666 square meters of construction area on 118,667 square meters (approximately 178 acres) of land. This includes building a recycled polyester workshop, a sorting workshop for waste polyester textiles, raw material warehouses, a comprehensive office building, etc. By purchasing catalyst preparation systems, alcoholysis reactors, pre-polycondensation reactors, final polymerization reactors, drum dryers, extruders, spinning machines, air compressors, spinning equipment, and false-twist texturizers, a 100,000-ton/year reclaimed polyester new material engineering project will be established. The main process flow is as follows: Waste polyester (PET) textiles → Alcoholysis → Liquid phase viscosity increase → Regenerated polyester chips → Pre-crystallization, drying → Melting and spinning → High-speed winding → Recycled polyester POY → Texturizing → DTY filament. Supporting public and auxiliary projects will also be built. In phase two, an additional investment of 3.9 billion yuan is planned, purchasing 192,000 square meters (approximately 288 acres) of land to increase production capacity by another 400,000 tons/year of reclaimed polyester textile new materials.
As a key industrial project in Hongze District, Huai'an City, the first phase of Jiangsu Lüsi Ke Lai New Materials Co., Ltd.'s annual production of 500,000 tons of recycled polyester new materials project is expected to be fully operational by June 2026. Upon reaching full production, the project is expected to achieve an annual sales revenue of 6 billion yuan and a tax revenue of 180 million yuan, providing strong support for Hongze District to build a leading national base for recycled polyester new materials.
Sateri's annual production project of 300,000 tons of lyocell fiber
On March 7, the Silver Syndicate for the first phase of the 300,000-ton Lyocell fiber project by Sateri (Shandong) Fiber Co., Ltd. was signed.
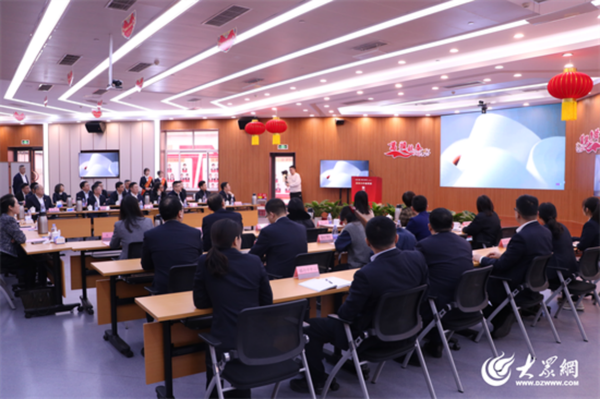
It is understood that the project is located in Yutai County, Jining City, and is invested and constructed by the Sateri Group under the Singapore-based Royal Golden Eagle Group. With a total investment of 11 billion yuan, the project has been included in the 8th batch of major foreign investment projects by the National Development and Reform Commission. The first phase of the project is led by the Industrial and Commercial Bank of China (ICBC) Jining Branch, which has formed a syndicate with eight other banks, including the Export-Import Bank of China, China Construction Bank, Agricultural Bank of China, Bank of Communications, Postal Savings Bank of China, Shanghai Pudong Development Bank, and China Minsheng Bank. This collaboration has achieved the "Spring Festival Acceleration," setting records for the fastest approval speed, the shortest syndication closure time, and synchronized fund disbursement and construction progress.
It is reported that the project adopts the NMMO solvent closed-loop system independently developed by Sateri. In the production of Lyocell fiber, the NMMO solvent closed-loop system achieves efficient recycling through multi-effect evaporation and intelligent control technology: the washing wastewater is cooled, and impurities are removed by flotation, then concentrated by ion exchange and six-stage evaporation (with progressively reduced pressure), eventually recovering NMMO monohydrate with a purity of 99.7%. The degradation product N-Methylmorpholine (NMM) is regenerated into NMMO by adding H₂O₂ for oxidation, while inhibitors such as propyl gallate reduce solvent degradation.
Upon full operation, the project is expected to generate an annual revenue of 10.4 billion yuan and create over 2,000 jobs. The plan includes the construction of four globally largest single-line cellulose material production lines, which will attract and cluster a group of upstream and downstream enterprises, forming a 50-billion-yuan textile new materials industrial cluster, leading the development of new productive forces in the textile industry.
Hengxin Green Technology Co., Ltd. CR Project
On March 5, 2025, the Fuzhou Ecology and Environment Bureau announced the public notice regarding the proposed approval decision for the environmental impact assessment document of the construction project. The project is located in the Kemen Economic Development Zone of Lianjiang, Fuzhou City, and plans to build a production line for melting and depolymerizing waste fishing nets and other waste nylon products to produce regenerated polyamide 6 (PA6) chips, with an annual output of 7,000 tons of fully opaque regenerated PA6 chips.
The CR project of Fujian Hengxin Green Technology Co., Ltd., a subsidiary of Hengshen Group, is centered on the group's independently developed nylon chemical recycling technology. It aims to establish a closed-loop recycling system for regenerated nylon T2T. Leveraging the pilot-scale verification already completed by the group, the project is being implemented on an engineering scale at the Shenyuan Integrated Industrial Park.
The first phase of the project, expected to commence production in the first quarter of 2026, will establish a production capacity of 7,000 tons of chemically regenerated nylon, filling the gap in the domestic nylon T2T recycling sector. With a total investment of 379 million RMB, the project's long-term capacity is projected to reach 100,000 tons, showcasing Hengshen Group's unwavering commitment to sustainable development.
The production in 2025 is expected to exceed 20 million tons.
The green and low-carbon transformation of the textile and apparel industry is urgently needed. According to data from the United Nations Environment Programme, the carbon emissions of the textile and apparel industry account for 10% of global carbon emissions, exceeding the combined emissions of all flights and maritime shipping. Projections indicate that by 2030, when the global population reaches 8.5 billion, the carbon emissions of the textile and apparel industry may surpass those of the petroleum industry, becoming the largest source of carbon emissions. By 2050, the fashion industry is expected to consume over 30% of the global carbon budget. China's "Implementation Opinions on Accelerating the Recycling of Waste Textiles" sets targets for a 25% recycling rate and an annual production of 2 million tons of recycled fibers by 2025, with the recycling rate increasing to 30% by 2030.
Additionally, the annual production capacity of regenerated cellulose fiber in 2023 was 7.8 million tons, and it is expected to increase to 10 million tons by 2025 (accounting for over 60% of the global total production capacity).
In the field of recycled polyester, the market production scale of recycled polyester staple fiber in 2023 was 4.7 million tons, of which the production of conventional recycled polyester staple fiber was 1.88 million tons. It is projected to exceed 8 million tons by 2025. Including other recycled fibers such as recycled nylon and recycled spandex, China's total recycled fiber production may surpass 20 million tons by 2025. Recycled fiber is not just the present but even more so the future!
【Copyright and Disclaimer】The above information is collected and organized by PlastMatch. The copyright belongs to the original author. This article is reprinted for the purpose of providing more information, and it does not imply that PlastMatch endorses the views expressed in the article or guarantees its accuracy. If there are any errors in the source attribution or if your legitimate rights have been infringed, please contact us, and we will promptly correct or remove the content. If other media, websites, or individuals use the aforementioned content, they must clearly indicate the original source and origin of the work and assume legal responsibility on their own.
Most Popular
-
Amcor Opens Advanced Coating Facility for Healthcare Packaging in Malaysia
-
ExxonMobil and Malpack Develop High-Performance Stretch Film with Signature Polymers
-
Plastic Pipe Maker Joins Lawsuit Challenging Trump Tariffs
-
Pont, Blue Ocean Closures make biobased closures work
-
Over 300 Employees Laid Off! Is Meina Unable to Cope?