Medical-grade high-end chemical materials: current situation and future
Medical-grade chemical materials come in many types, primarily可分为高分子、金属、无机非金属及复合材料, and they are mainly applied in areas such as medical devices, drug carriers, implant equipment, and more. Note: The phrase "可分为高分子、金属、无机非金属及复合材料" is directly translated to maintain the original structure, but for better readability in English, it might be more appropriate to rephrase it as "primarily分为 polymers, metals, inorganic non-metallic materials, and composite materials".
China has a large population and a vast and完善 medical system. The market size of medical materials has already exceeded one trillion yuan, with a compound annual growth rate exceeding20%Particularly in areas such as wound care and surgical consumables, large-scale application has already been achieved.
However, high-end medical materials have一直严重依赖进口, such as ultra-high molecular weight polyethylene and halogenated butyl rubber.75%Dependent on imports.
The production process of medical-grade materials and the international medical certification barriers severely restrict the localization process of medical materials.
In the country“Fourteen Five”Under the promotion of the new materials special project,COC/COPMaterials such as biodegradable polylactic acid have achieved technological breakthroughs; however, the industrial chain is still not complete, including raw materials, key processes and equipment, and quality control.“Bottleneck”The problem urgently needs to be solved.
Today, we will analyze the current status, challenges, and future pathways of domestic medical materials from the perspectives of technological breakthroughs and industrial upgrades.
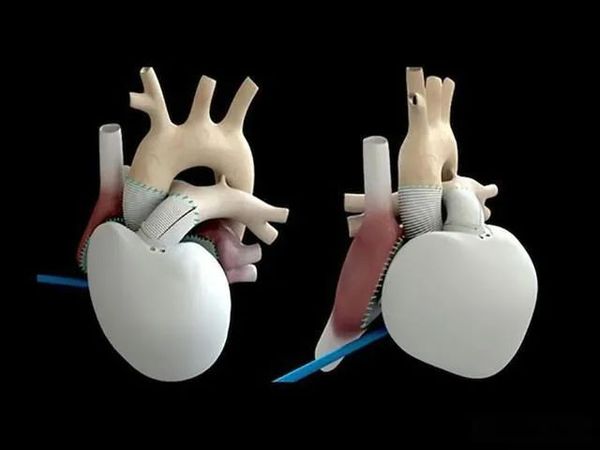
I, Medical chemical materials include which ones? (Note: The original Chinese sentence seems to be incomplete or incorrectly phrased. A more accurate translation of the intended meaning would be: "I. What are the types of medical chemical materials?")
Classification of Medical Materials
Medical chemical materials are a type of functional materials with special properties such as biocompatibility and corrosion resistance, widely used in medical devices, drug carriers, implantable devices, and other applications.
According to material category, they can be roughly divided into three types.
Polymer materials (accounting for medical materials)60%): including polyurethane, silicone rubber, polylactic acid (PLA), polyether ether ketone (PEEK, can be applied in areas such as artificial organs and surgical supplies.
Inorganic non-metallic materials, such as bioceramics and glass, are commonly used in orthopedic and dental implants.
Metals and composite materials, such as titanium alloys and carbon fiber reinforced polymers, are commonly used in cardiovascular stents and high-load implantable devices.
The market size is very large.
2024In 2023, the scale of China's medical device market has reached1090010 billion yuan, among which the market size for medical polymer materials exceeds3000Billion yuan, with a compound annual growth rate of31.55%。
Biomaterials have been listed as a national“Fifteen-fourteen”Key directions2024The industry's R&D investment has also increased this year.8.2%Above all, the industrial chain upgrade driven by policies will accelerate.
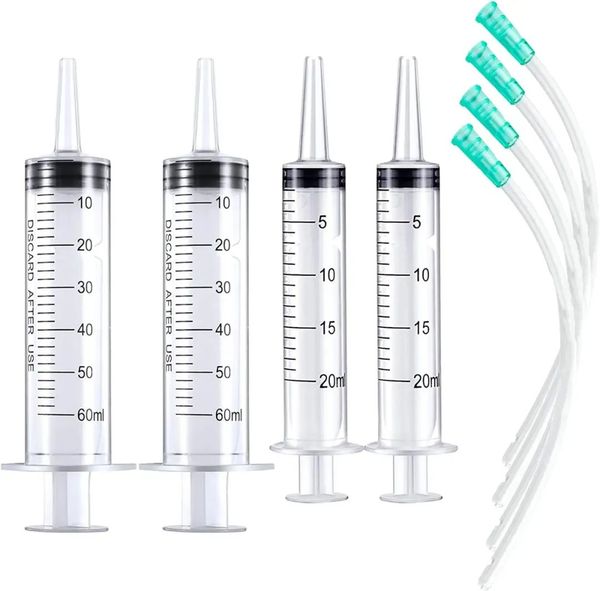
II. Comparison of Production Patterns at Home and Abroad
Current Status of International Monopoly
High-end medical materials have long been monopolized by foreigners: ultra-high molecular weight polyethylene is mainly controlled by Celanese of Germany and DSM of the Netherlands.DSMMonopoly; The import dependence on halogenated butyl rubber (vaccine stopper material) exceeds70%。
Higher technical barriers: Medical-grade materials have strict requirements for molecular weight and impurity content (such as heavy metals).<0.1ppmThe requirements for the ) products are more stringent than those for conventional products, and many production technologies, core catalysts used in reactions, and key production equipment are monopolized by international giants through patents.
Domestic technological breakthroughs
Medical Polyolefin: Lanzhou Petrochemical has built the country's first clean production facility for medical polypropylene, and some grades developed can replace imported materials for upright infusion bags.
COC/COPMaterials: Acuity and TuoXing Technology have successfully broken through the synthesis technology of isoprene monomer.
Acrylic thousand-ton level high transparency material (Cyclic olefin copolymer)COCThe production facility, which has been completed,24Production trials have already begun at the end of the year.
TuoXian Technology Phase I3000ton/YearCOC/COPProduction facility2023year6Completed and put into production in the same month, the products have already started to enter the market, with a transparency rate of (>).92%It has reached international standards and can be used in vaccine packaging and optical lenses.
Biodegradable materials: Ordinary absorbable suture products can be produced on a large scale by domestic companies, such as polyglycolic acid and polylactic acid.PGLASutures and other items, the production cost is that of imported products.60%-70%。
However, its products mainly focus on low to medium molecular weight products, and there is still a certain gap in the precise control of degradation speed and mechanical strength compared to imported products.
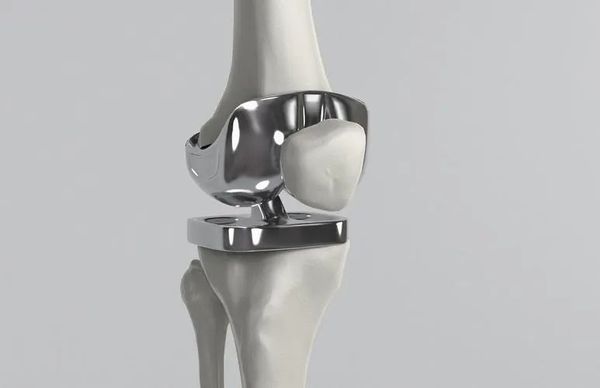
III. Core Challenges in the Process of Domestication
Technical bottleneck
Ingredients“Stranglehold”The dicyclopentadiene monomer is used for production.COC/COPMain raw material, high purity/Medical-grade materials are mainly reliant on imports, with companies like Mitsubishi Chemical and Mitsui Chemicals dominating the market.80%The above market share. Isobutylene monomer accounts forCOC/COPTotal cost of60%, resulting in relatively high production costs for enterprises; ultra-pure5NLevel (≥99.999%Quartz sand, which is an raw material for vaccine vials, has a domestication rate of less than 30%.20%。
Insufficient process accuracy: DomesticPLAThe degradation rate of sutures fluctuates within the range of.±20%Imported products can be controlled at.±5%Within the domestic range, domesticallyPLAFiber strength is0.6-0.8GPaFails to meet the standards of imported products.1.2GPa, resulting in low suture tension retention after surgery.
The purity of domestic isobutylene monomer is99%Imported products can achieve99.9%, leading toCOCThe fluctuation range of transmittance is relatively wide.±2%Import±0.5%)。
Medical Useα-The curing time deviation of domestically produced cyanoacrylate adhesives.±10Seconds, imports can already be controlled at±3Seconds.
Market and Certification Barriers
The international certification cycle for medical products is long.FDA、CEAuthentication takes approximately需要提供具体时间或者更多上下文以给出准确翻译。3-5In the year, the cost of certification exceeded ten million, and domestically there were only10%The company has passed the certification.
Medical Institution Usage Habit: Top Tertiary Hospitals in China90%For high-value consumables (such as artificial joints), imports are prioritized, while domestic products are placed in the second tier due to insufficient performance in biocompatibility, corrosion resistance, or mechanical strength.
Shortcomings in Industry Chain Coordination
Insufficient upstream-downstream collaboration: For example, orthopedic materials need to match the corresponding surgical instrument design, but domestic companies have barely any.“Material-Device-Clinical”The joint R&D system has led to a situation where even with suitable materials available, they cannot be practically applied.
Equipment relies on imports: continuous polymerization reactors, solid-liquid separation equipment, stripping equipment, crystallization equipment, high-precision injection molding machines, and other key equipment.90%Still requires imports. Some domestic companies can produce, but their performance, efficiency, adaptability, and after-sales service do not yet meet the standards of foreign companies.
Summary and Outlook
Domestic medical chemical materials are already at “From quantitative change to qualitative change” The critical point in polyolefins,COC/COPMid-range products are already in mass production, and the situation of relying on imports for high-end products won't last much longer.
With the strong support of national policies (such as“New Materials Special Project”Billion-dollar funds and the continuous iteration of technologies among production enterprises.AI+(nano-modification), expected2030The localization rate of high-end medical products is expected to increase to.60%That is all.
【Copyright and Disclaimer】The above information is collected and organized by PlastMatch. The copyright belongs to the original author. This article is reprinted for the purpose of providing more information, and it does not imply that PlastMatch endorses the views expressed in the article or guarantees its accuracy. If there are any errors in the source attribution or if your legitimate rights have been infringed, please contact us, and we will promptly correct or remove the content. If other media, websites, or individuals use the aforementioned content, they must clearly indicate the original source and origin of the work and assume legal responsibility on their own.
Most Popular
-
Four Major Chemical New Material Giants Sell Off and Shut Down Again!
-
Covestro faces force majeure!
-
DuPont to Spin Off Nomex and Kevlar Brands for $14.4 Billion: Is Aramid Fiber Still Attractive?
-
Massive Retreat of Japanese and Korean Battery Manufacturers
-
Napan Unveils Thermoplastic Composite Three-in-One Power System Solution, Battery Cover Weight Reduced by 67%