Shaanxi University of Technology: The Effect of Organic Fluorescent Materials on the Properties of Photosensitive Polyimide
Engineering Plastics Applications
2025-03-28 15:19:44
Abstract: Using 2,2-bis(3-amino-4-hydroxyphenyl)hexafluoropropane, 5-amino-2-(4-aminophenyl)benzimidazole, and 3,3',4,4'-diphenyl ketone dianhydride as main raw materials, a photosensitive polyimide (PSPI) prepolymer was synthesized. The prepolymer was then thoroughly mixed with four different fluorescent materials containing dithioglycolic acid and coated into films, followed by UV curing, resulting in five groups of PSPI film samples, including a control group. The performance of each PSPI film was characterized using Fourier transform infrared spectroscopy, universal testing machine, differential scanning calorimetry, and contact angle goniometer. The water contact angle and water absorption rate of the PSPI films were studied. The results indicated that although PSPI films containing characteristic functional groups of polyimide were successfully synthesized, the tensile strength of the PSPI films with fluorescent materials was slightly lower than that of the PSPI films without fluorescent materials, while the glass transition temperature increased. This suggests that the addition of fluorescent agents increases the side chain volume of PSPI molecules and alters their symmetry, reducing molecular flexibility. The fluorescent materials also increased the structural voids in PSPI molecules, resulting in better hydrophilicity and water absorption.
Polyimide (PI) is a type of polymer that contains cyclic imide rings in its molecular chain. Compared to other inorganic non-metal materials, PI has excellent high-temperature resistance and flame retardancy, with a decomposition temperature of 500-600 °C and a long-term use temperature of 200-380 °C. It possesses outstanding mechanical properties, including high strength and high modulus, as well as good creep resistance, dimensional stability, weather resistance, and corrosion resistance. However, PI usually requires high thermal curing temperatures, and the molding conditions are stringent. Photosensitive polyimide (PSPI) contains photosensitive units in its molecular chain that can achieve polymerization through photochemical cross-linking reactions under specific energy light exposure; PSPI not only reduces the polymerization temperature of PI but also accommodates various processing techniques.
Fluorescence is the light emitted by a substance after it absorbs light or other electromagnetic radiation. When the absorption intensity is high, a two-photon absorption phenomenon may occur, leading to the emission of radiation at a wavelength shorter than the absorption wavelength. Fluorescent materials are substances that can absorb light of a specific wavelength and emit light at another wavelength. Utilizing this property of fluorescent materials, suitable dianhydrides and diamines are selected, and substances with photosensitive active groups are added to obtain PSPI prepolymers under certain conditions. Four types of organic fluorescent materials, self-made in the laboratory, are uniformly dispersed in the PSPI prepolymers, followed by film coating and ultraviolet curing. The effect of organic fluorescent materials on the curing of PSPI is explored, and further investigation is conducted on the physical and chemical properties of PSPI after the addition of organic fluorescent materials, providing new research ideas for the rapid curing of PSPI.
N-Methylpyrrolidone (NMP), 2,2-bis(3-amino-4-hydroxyphenyl)hexafluoropropane (6FAP), 5-amino-2-(4-aminophenyl)benzimidazole (BIA), 3,3',4,4'-benzophenone tetracarboxylic dianhydride (BTDA), triethylamine, glycidyl methacrylate (GMA), hydroquinone, photoinitiator Irgacure 819, polyethylene glycol diacrylate (PEG400DA), 1-vinyl-2-pyrrolidone (NVP): analytical grade, Shanghai Aladdin Biochemical Technology Co., Ltd.
Fluorescent material: homemade in the laboratory.
1.2 Main Instruments and Equipment
Electronic tensile testing machine: AI-7000-MU2, high-speed rail testing equipment (Dongguan) Co., Ltd.
Differential Scanning Calorimeter (DSC): DSC1, Mettler-Toledo, Switzerland;
UV Curing Forming Machine: UV-030A, Shenzhen Daye Laser Forming Technology Co., Ltd.
1.3.1 Preparation of PI-GMA
Dissolve 6FAP completely in NMP, add a quantitive amount of BIA, and stir for 2 hours under a nitrogen atmosphere to ensure uniform dispersion of the two monomers. Under ice-water bath conditions, add a quantitive amount of BTDA to the conical flask and continue reacting for 5 hours in a nitrogen atmosphere. After purging with nitrogen, seal the flask and place it in the refrigerator to react for more than 16 hours. Transfer the reactants to a hydrothermal reactor, purging with nitrogen and sealing it. Place the reactor in an oven and increase the temperature of the reaction system with the following specific temperature program: 120 °C for 1 hour, 160 °C for 1 hour, and 200 °C for 4 hours, resulting in a brown-red viscous liquid. After cooling to room temperature, pour the reactants into a conical flask, stirring while adding a quantitive amount of triethylamine, followed by a quantitive amount of GMA, and finally a quantitive amount of hydroquinone. Increase the temperature of the system and react at 100 °C for 5 hours. Once the solution cools to room temperature, precipitate in ethanol, filter, and dry in a vacuum oven for 24 hours to obtain a light yellow PI-GMA powder, with the specific formulation shown in Table 1.
Table 1 Raw material formula of PI-GMA g
1.3.2 Preparation of Fluorescent Materials
Mix urea and salicylic acid in a molar ratio of 1:1.5, and heat the mixture at 70 °C for 48 hours to obtain blue carbon dot fluorescent materials; mix urea and thiosalicylic acid in a molar ratio of 1:0.25, and heat the mixture at 180 °C for 10 hours to obtain green carbon dot fluorescent materials; mix urea and thiosalicylic acid in a molar ratio of 1:1, and heat the mixture at 180 °C for 10 hours to obtain yellow fluorescent materials; mix urea and dibenzothiophene-5,5-dioxide in a molar ratio of 1:0.25, and heat the mixture at 180 °C for 10 hours to obtain red fluorescent materials.
1.3.3 Preparation of PSPI Films
In a brown conical flask, a quantitative amount of NVP was added, followed by the addition of PI-GMA powder and PEG400DA, stirring until uniform. Finally, the photoinitiator Irgacure 819 was added, and the mixture was stirred in the dark for 2-3 hours until homogeneous, resulting in a uniform viscous transparent solution (PSPI prepolymer). A quantitative amount of organic fluorescent material was added to the PSPI prepolymer, and it was stirred in the dark for 30 minutes to obtain a viscous transparent mixture of fluorescent material/PSPI. The total amount of each mixture ratio was 20 g. After drying the mixture into a film, it was cured under UV light for 2 hours, resulting in a PSPI film (formulation shown in Table 2). At this point, the film's surface was smooth, non-tacky, and indistinguishable from films cured for more than 3 hours (as shown in Figure 1).
Tab. 2 Raw material ratio of PSPI film %
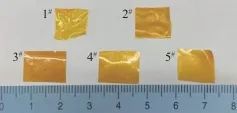
Fig. 1 Appearance of PSPI film
1.4.1 Structural Analysis
Cut the sample into a 2 cm × 2 cm film and fix it in the designated area of the FTIR spectrometer, allowing infrared light to pass through the film. After imaging the infrared spectrum on the electronic device, export the selected wavelength range for analysis.
1.4.2 Mechanical Performance Analysis
Using an electronic tensile testing machine to test the tensile strength and elongation at break of the samples. The samples are cut into strips of 5 cm × 1 cm, and the thickness at both ends and the middle of each strip is measured to take the average value and record the data. The strips are fixed in the clamps of the computer-controlled tensile testing machine, and the distance between the upper and lower clamps is measured and recorded. The strips are subjected to tensile testing at a speed of 5 mm/min. After the computer calculates the tensile strength and elongation at break, the data is compared for tensile performance analysis.
The glass transition temperature (Tg) of the sample is measured using a DSC instrument. Take 3-6 mg of the sample, with a heating rate of 20 °C/min, and a temperature range of 25-300 °C.
1.4.4 Analysis of Water Wettability
The wettability of the sample was measured and analyzed using a contact angle measuring instrument. The sample was fixed horizontally on the equipment platform, and distilled water was dropped onto the surface of the sample. After 20 seconds, the shape of the distilled water on the sample was instantaneously captured using the built-in camera of the device. The captured images were processed using analysis software to obtain the contact angle data of each sample with distilled water for further analysis.
1.4.5 Water Absorption Analysis
According to GB/T 1033.1-2008 for testing, the sample is cut into strips measuring 6 cm × 2 cm, and the weight is recorded. Then, each strip is completely immersed in distilled water for 6 hours. After wiping off the surface moisture, the strips are air-dried and weighed again, with the data recorded. The water absorption rate of each sample is calculated based on the weight before and after water absorption. The water absorption rate = (m2 - m1) / m1 × 100%, where m1 is the weight of the cured film before soaking, and m2 is the weight of the cured film after water absorption.
2.1 FTIR Structural Analysis
According to the information available [13-14], the characteristic functional groups of PSPI are located near 718 cm-1 (deformation vibration of amide C=O), near 1,370 cm-1 (stretching vibration of amide C—N—C), and near 1,780 cm-1 (asymmetric stretching vibration of amide C=O). If the characteristic functional groups of PSPI appear near these three vibration bands, it is sufficient to prove the successful imidization of the sample.
Figure 2 shows the FTIR spectrum of PSPI films. As shown in Figure 2, the PSPI film without fluorescent materials has distinct vibration peaks at 1,760 cm-1, 1,350 cm-1, and 790 cm-1; film 1 has distinct vibration peaks at 1,750 cm-1, 1,330 cm-1, and 781 cm-1; film 2 has distinct vibration peaks at 1,750 cm-1, 1,340 cm-1, and 787 cm-1; film 3 has distinct vibration peaks at 1,750 cm-1, 1,330 cm-1, and 785 cm-1; film 4 has distinct vibration peaks at 1,756 cm-1, 1,340 cm-1, and 781 cm-1. The above vibration peaks are all within the vibration bands of the characteristic functional groups of PSPI, indicating that the samples have all undergone imidization. From Figure 2, it can also be seen that there are distinct absorption peaks at 810 cm-1 and 1,635 cm-1, with 900 cm-1 corresponding to the out-of-plane bending absorption peak of —C=C—, and 1,559 cm-1 corresponding to the stretching vibration peak of —C=C—, indicating that the photosensitive units have been successfully grafted onto the long chain of PSPI.
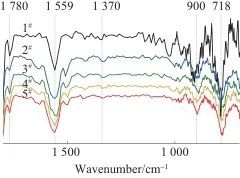
Fig. 2 FTIR spectra of PSPI films with different ratios
2.2 Stretching Performance Analysis
Figure 3 compares the average elongation at break and tensile strength of PSPI films with different ratios, while Figure 4 shows the elongation at break and tensile strength curves of PSPI film samples with different ratios. Comparing the five sets of data in Figure 3, it can be observed that the tensile strength of PSPI films with added fluorescent materials is slightly lower than that of PSPI films without fluorescent materials. This indicates that the organic fluorescent materials reduce the crystallinity and orientation of PSPI, thereby decreasing the flexibility of PSPI molecular chains, which ultimately results in a reduction in tensile strength.
At the same time, observing the elongation at break of the five samples reveals that the elongation at break of PSPI films with organic fluorescent materials is significantly lower than that of PSPI films without fluorescent materials. This further confirms that the addition of fluorescent materials increases the entanglement between PSPI molecular chains, leading to the stiffening of the molecular chains. Due to the low reactivity of the structural units in PSPI, it is not easy to achieve photopolymerization; therefore, a relatively high amount (7%) of photoinitiator was added. However, excessive photoinitiator can generate too many free radicals during the reaction, adversely affecting the formation of macromolecular chains. As indicated by the tensile strength, the PSPI films ultimately exhibit a decrease in tensile strength. To resolve this contradiction, further exploration is needed to find the optimal ratio.
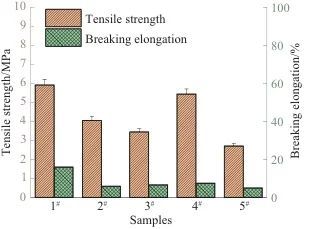
Fig. 3 Comparison of elongation at break and tensile strength of PSPI films with different ratios
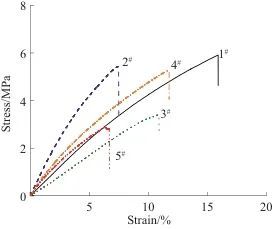
Fig. 4 Curves of tensile stress-strain of PSPI films with different ratios
Tab. 3 Tg comparison of five PSPI films
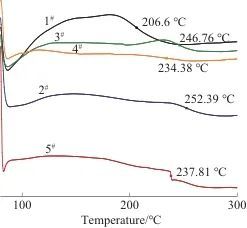
Fig. 5 DSC curves of five PSPI films
2.4 Analysis of Water Wettability
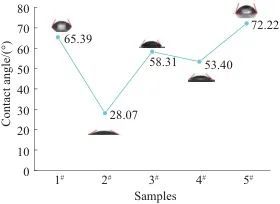
Fig. 6 Comparison of five PSPI films contact angles
2.5 Water Absorption Analysis
Figure 7 compares the water absorption rates of five types of PSPI films. From Figures 6 and 7, the following conclusions can be drawn: among the five samples, the smaller the water contact angle, the better the hydrophilicity and water absorption of the film; conversely, the larger the water contact angle, the poorer the hydrophilicity and water absorption of the film. Sample 2# and 4# exhibit slightly higher water absorption compared to the PSPI without fluorescent materials, which is because the fluorescent materials added to 2# and 4# contain dithiosalicylic acid, which has a higher water absorption capacity. Additionally, after the addition, it reacts with the side groups of PSPI, leading to a decrease in crystallinity and an increase in structural gaps, creating more space for water retention. In the other two samples, the fluorescent materials contain thiosalicylic acid, which is slightly soluble in water, but the fluorescent material in 3# contains a certain amount of hydrophilic formamide, while 5# does not contain any hydrophilic groups, resulting in 5# exhibiting the lowest water absorption rate.
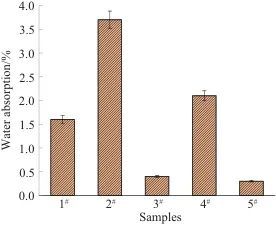
Fig. 7 Comparison of water absorption rate of five PSPI films
(1) Four different colors of organic fluorescent materials were synthesized and added to the self-synthesized PSPI prepolymer. These resins can cure under ultraviolet light to form PSPI films. FTIR analysis showed that all five PSPI films exhibited characteristic peaks of PSPI. The addition of organic fluorescent materials affects the crystallinity, orientation, and flexibility of the PSPI molecules, resulting in a decrease in both the tensile strength and elongation at break of the films. The inclusion of fluorescent agents increases the volume of the side groups of the PSPI molecules and alters their symmetry, reducing molecular flexibility, which leads to an increase in the Tg of the PSPI films compared to those without fluorescent materials. Hydrophilicity and water absorption tests revealed that the fluorescent material containing dithiosalicylic acid reduced the crystallinity of the PSPI molecules and increased structural voids, resulting in better hydrophilicity and water absorption.
(2) Although fluorine-containing monomers were used, in order to improve the light-curing properties of the prepolymer, NVP was used as the solvent when preparing the PSPI film, resulting in the cured PSPI film being brown and having strong light absorption. None of the five PSPI films exhibited fluorescence effects after exposure to ultraviolet light. The added fluorescent materials are small organic molecules, which can reduce the toughness of PSPI and alter the water absorption properties of the film. Further experimental validation is needed for the study of PSPI modified with fluorescent materials.
【Copyright and Disclaimer】The above information is collected and organized by PlastMatch. The copyright belongs to the original author. This article is reprinted for the purpose of providing more information, and it does not imply that PlastMatch endorses the views expressed in the article or guarantees its accuracy. If there are any errors in the source attribution or if your legitimate rights have been infringed, please contact us, and we will promptly correct or remove the content. If other media, websites, or individuals use the aforementioned content, they must clearly indicate the original source and origin of the work and assume legal responsibility on their own.