The "Up and Down Debate" of 7-Layer Co-Extrusion Film Equipment
One, the core difference between upper blowing and lower blowing equipment is the direction of airflow determining the process characteristics.
The essential difference between up-blowing and down-blowing equipment lies in the design of bubble cooling direction. Up-blowing equipment uses a vertically upward inflation method, where the bubble cools naturally as it rises, with the cooling air ring typically located below the die. In contrast, down-blowing equipment employs vertical downward inflation, with the cooling air ring directly enveloping the die, rapidly cooling the bubble through water cooling or strong air flow. This difference results in significant distinctions in process control and product performance between the two methods.
1.Cooling efficiency and crystallinity
The downward-blowing equipment has a more direct contact between the cooling medium (water or cold air) and the membrane bubble, resulting in a cooling rate that is 30%-50% faster than upward-blowing equipment. This effectively suppresses excessive crystal growth and improves the transparency and gloss of the film. In contrast, the natural cooling process of the upward-blowing equipment is more beneficial for the directional arrangement of molecular chains, enhancing the longitudinal tensile strength of the film.
2. Thickness uniformity
In downward-blown equipment, the film bubble extends vertically downward under gravity, reducing issues with uneven lateral tension, and the thickness deviation can be controlled within ±3%. In contrast, upward-blown equipment is more susceptible to environmental airflow disturbances as the film bubble rises, resulting in thickness uniformity typically around ±5%.
3. Production capacity ceiling
The water cooling system of the down-blowing equipment supports a higher expansion ratio (up to 1:6) and faster drawing speeds (line speeds exceeding 30m/min). The annual production capacity of a single unit can reach 15,000 tons, while the up-blowing equipment is limited by cooling efficiency, with an annual production capacity of usually below 8,000 tons.
4. Cooling methods and transparency
Upstream blowing equipment: uses air cooling (such as IBC internal cooling system), the cooling speed is relatively slow, which may lead to a certain degree of stretching in the arrangement of the film molecules, resulting in relatively low transparency. However, through improved die design and parallel multi-channel technology, it can approach the transparency of cast films.
Bottom-blowing equipment: Utilizes water-cooling technology, offering rapid cooling and more orderly molecular alignment, resulting in high film transparency, particularly suitable for packaging requiring high transparency (such as food vacuum packaging).
Extrusion Volume and Production Efficiency
The upward-blowing equipment, due to the stability of its air-cooling system, is typically suitable for large-scale production of high-barrier films, offering high extrusion output, lower equipment investment costs, and minimal material waste.
The down-blow equipment is limited by the water cooling process, resulting in slightly lower extrusion rates, but it is more suitable for producing films with high tensile strength and puncture resistance (such as films containing PA or EVOH barrier layers).
Performance Difference
Bubble film: Due to the stretching during the blowing process, there is a significant difference in the longitudinal and lateral molecular orientation, which may affect the heat seal performance and temperature resistance. However, through a seven-layer independent temperature control design (such as a planar stacking die head), the barrier properties and functional layer distribution can be optimized, making it suitable for high-functionality scenarios such as greenhouse films.
Down-blow film: More uniform cooling and shaping, higher tensile strength, better puncture resistance, and more stable performance of the barrier layer (such as PA in the middle layer). Suitable for high-demand fields such as vacuum packaging and medical applications.
II. Finished Product Market Applications
Food Packaging:
The downward-blowing high transparent film is used for vacuum packaging (such as meat and seafood), blocking oxygen and moisture to extend shelf life.
The seven-layer blown film achieves functional layering (such as adding slip agents in the inner and outer layers and a barrier layer in the middle), making it suitable for frozen food packaging and high-temperature cooking applications.
2. Agriculture:
The seven-layer co-extruded greenhouse film enables multifunctional stacking (such as light conversion, insulation, and anti-drip anti-fog), enhancing crop yield.
3. Pharmaceuticals and Cosmetics:
- The high barrier property of downward blown film is used for moisture-proof packaging of medicines, while upward blown film avoids material decomposition through independent temperature control, making it suitable for encapsulating sensitive components.
4. Industry and Construction: The building membranes produced by upward-blowing equipment (such as waterproof and thermal insulation membranes) are low in cost, while downward-blowing membranes are used for high-weather-resistance decorative materials.
Three, Performance Parameter Comparison: The Technological Gambit Behind the Numbers
IV. Market Application: Technical Characteristics Determine Value Positioning
High-end food packaging
2. Medical device packaging
Industrial Special Film
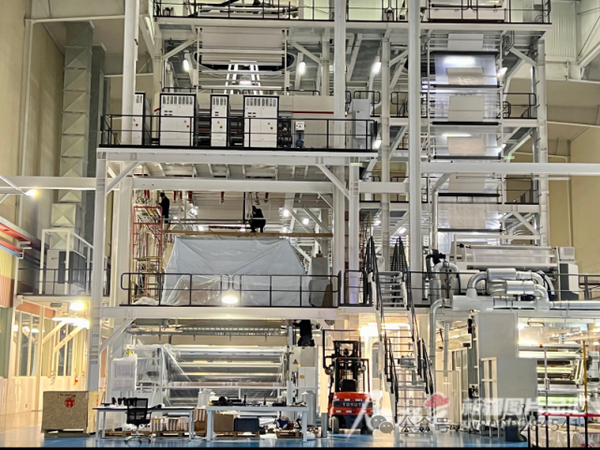
The current industry is undergoing technological iteration:
Downdraft equipment
Blowing equipment
This decades-long "top vs. bottom debate" is essentially a comprehensive contest among materials science, fluid mechanics, and intelligent control. With the increasing application of bio-based materials (such as PLA, PHA), the two technological pathways may engage in a new competitive chapter in the field of biodegradable co-extruded films.
【Copyright and Disclaimer】The above information is collected and organized by PlastMatch. The copyright belongs to the original author. This article is reprinted for the purpose of providing more information, and it does not imply that PlastMatch endorses the views expressed in the article or guarantees its accuracy. If there are any errors in the source attribution or if your legitimate rights have been infringed, please contact us, and we will promptly correct or remove the content. If other media, websites, or individuals use the aforementioned content, they must clearly indicate the original source and origin of the work and assume legal responsibility on their own.
Most Popular
-
Amcor Opens Advanced Coating Facility for Healthcare Packaging in Malaysia
-
ExxonMobil and Malpack Develop High-Performance Stretch Film with Signature Polymers
-
Plastic Pipe Maker Joins Lawsuit Challenging Trump Tariffs
-
Pont, Blue Ocean Closures make biobased closures work
-
Over 300 Employees Laid Off! Is Meina Unable to Cope?