What are the key indicators of ultrafine calcium carbonate? How should one select ultrafine calcium carbonate suitable for plastic use targetedly?
For ultrafine calcium carbonate, particle size, specific surface area, crystal form, and oil absorption value are the most important technical indicators that directly affect the application performance of ultrafine calcium carbonate.
Of course, this does not deny the importance of other indicators, but other indicators are relatively easier to achieve in the industry.
However, for specialized products, the purposes are different, and the emphasis on various technical indicators of ultrafine calcium carbonate varies accordingly, with different requirements that cannot be treated the same way.
Particle size and specific surface area
How to achieve an average particle size of 0.02~0.1μm for primary particles of ultrafine calcium carbonate is a fundamental indicator for ultrafine calcium carbonate, and it is undoubtedly crucial. Otherwise, it cannot be called ultrafine calcium carbonate.
Strictly speaking, this only completes half of the task of producing ultrafine calcium carbonate. If the surface treatment technology and dispersion technology do not keep up, it will cause the generated primary particles to agglomerate into large secondary particles, with particle sizes reaching several hundred nanometers.
Therefore, the photos observed or taken under the transmission electron microscope (TEM) can only reflect the size of the primary particles and cannot represent the actual particle size of the secondary particles after aggregation (due to certain technical treatments during the sample preparation process). This severely aggregated ultrafine calcium carbonate has a relatively small specific surface area measured by BET.
Therefore, only by using transmission electron microscopy in conjunction with specific surface area measurement can a more scientific and comprehensive judgment be made regarding the fineness of ultrafine calcium carbonate, the morphology of the particles, and their dispersion status.
The average particle size of ultrafine calcium carbonate is intrinsically related to its specific surface area. Some researchers use sedimentation volume to determine particle size. As is well known, factors affecting the sedimentation volume of calcium carbonate include not only particle size (which is influenced by limestone quality, lime calcination quality, lime digestion, carbonation conditions, etc.) but also the crystal form of calcium carbonate. Moreover, calcium carbonate exhibits diverse crystal forms, and even the same crystal form may vary due to its irregular geometric morphology, making the impact of crystal form on sedimentation volume quite complex. Therefore, using sedimentation volume to determine particle size is not scientifically rigorous and can lead to significant errors.
To effectively prevent the agglomeration of secondary particles, ultrafine calcium carbonate generally requires surface modification treatment, as the surface treatment process not only effectively improves the activity of ultrafine calcium carbonate but also effectively prevents the agglomeration of secondary particles.
For a specific specialized grade of ultrafine calcium carbonate, to better meet user requirements, there are differences in crystal form and particle size, as well as choices in surface treatment agents, along with experience and know-how in the treatment process.
Therefore, it is difficult to use a uniform standard to evaluate ultra-fine calcium carbonate dedicated varieties for different uses.
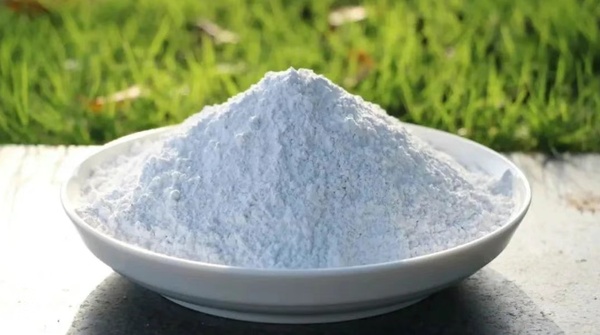
Crystalline form
For ultrafine calcium carbonate, crystal form is also a very important technical indicator.
It is well known that ordinary light calcium carbonate is spindle-shaped. When used in PVC plastics, it can generate significant stress, causing the plastic film to whiten. As for ultrafine calcium carbonate, it should produce products with different crystal forms based on different applications. For example:
Ultrafine calcium carbonate for plastics requires a simple crystal structure, smaller bulk volume, and lower oil absorption value, so cubic or spherical shapes are preferred. Ultrafine calcium carbonate with a particle size of 0.072 μm has a certain reinforcing effect on PVC plastics, making the surface of the products fine and glossy, with good electrical insulation performance. When used in soft cable materials, it can maintain its properties in accordance with national standards even when the filling amount is increased more than twofold. When used in plastic films, it can reduce whitening and improve low-temperature elongation. When used in rigid plastics, such as plastic doors and windows and various profiles, it can enhance the impact resistance, making the notched impact strength reach 49.1 kJ/m².
Ultrafine calcium carbonate for rubber, the chain-like type has the best reinforcing performance. Chain-like ultrafine calcium carbonate is formed by several to dozens of calcium carbonate crystal grains bonded in one direction. It has a three-dimensional spatial structure in rubber, with excellent dispersibility. When mixed with rubber, the chains of calcium carbonate break, forming active surfaces that bond more firmly with the rubber chains, thereby significantly enhancing its reinforcing effect in rubber. The order of reinforcing performance of different shapes of ultrafine calcium carbonate in rubber, from strongest to weakest, is: chain-like, needle-like, spherical, and cubic.
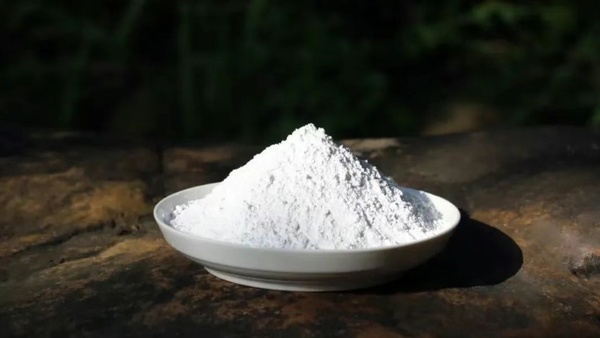
Ultrafine calcium carbonate used in ink is preferably cubic, which is determined by the nature of the ink. After filling ultrafine calcium carbonate in resin-based ink, it is required to have high gloss, good transparency, and good fluidity. The cubic shape is most beneficial to the gloss of the ink.
Precipitated calcium carbonate used in paper coating generally does not belong to the category of ultra-fine calcium carbonate, as its particle size is typically in the range of fine calcium carbonate (0.1 to 1 μm). However, there is one similarity: there are certain requirements for crystal form. For instance, requirements include opacity (covering power), high viscosity concentration, whiteness, and absorption performance with respect to ink. Therefore, tabular and cubic crystal forms are considered ideal.
In summary, it is not only necessary to ensure that the particle size of ultra-fine calcium carbonate is between 0.02~0.1μm, but also to determine the category of product crystal form based on its intended use, in order to produce marketable products.
Oil Absorption Value
The oil absorption value of ultrafine calcium carbonate is very important for its application performance, especially for plastics, coatings, and inks. For example, if the oil absorption value is high, it will consume a large amount of plasticizer when used in plastics; when used in coatings and inks, it will increase the viscosity. Therefore, the oil absorption value should not be too high.
In addition to the inherent physical properties of the material itself, there are many other factors that influence the oil absorption value of a certain powder, among which the particle size of the powder is a significant factor.
Therefore, as ultrafine calcium carbonate, the first consideration is the size of the ultrafine calcium carbonate particles, how well they disperse, and whether the specific surface area corresponds to the particle size. On this basis, we then consider how to reduce its oil absorption value; only in this way does it have practical significance. If its dispersibility is poor and secondary particle agglomeration is severe, resulting in a very small specific surface area, even if the oil absorption value is low, it will have no practical significance in application.
Main content
The main content (calcium oxide) of ultrafine calcium carbonate should not be strictly limited within a certain range. This is because, in most cases, ultrafine calcium carbonate is used as a functional filler, and what affects the filled material is usually its physical properties rather than chemical properties. Within a certain range, the main content of ultrafine calcium carbonate can meet the requirements for its physical properties.
In the preparation of ultrafine calcium carbonate, to obtain various crystal forms, good dispersibility, and excellent activation properties to meet the requirements of different products such as plastics, rubber, ink, etc., certain regulators, dispersants, surface treatment agents, and other additives are usually added. Generally speaking, these intentionally added "impurities" do not affect the application performance of ultrafine calcium carbonate; in fact, they may even be beneficial. However, due to the intentional addition of these so-called impurities, the main content (calcium oxide) of the ultrafine calcium carbonate is inevitably affected.
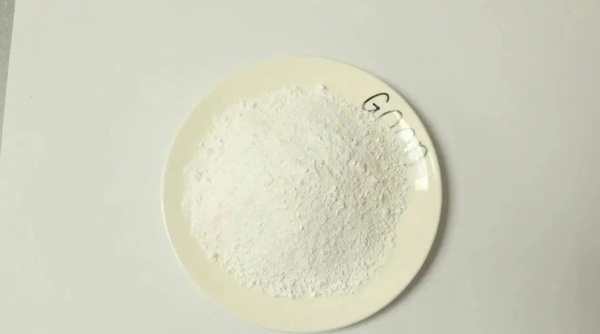
Of course, for certain harmful elements such as iron and manganese, whether they come from the raw materials or are introduced during the preparation process, they should be strictly controlled. These harmful impurities not only affect the color of the products but also accelerate the degradation of the resin itself, hastening the aging of the resin, and should be strictly avoided. Other impurities such as silicon, aluminum, and magnesium also adversely affect the whiteness of ultrafine calcium carbonate and can negatively impact the operations in the production process. Therefore, control should be exercised when selecting limestone raw materials.
It can be seen that for the main component of ultrafine calcium carbonate (calcium oxide), the requirements should not be too strict within an appropriate range, otherwise it will affect the development of some specialized varieties.
In summary, the key development directions for ultrafine calcium carbonate are specialization, series development, multi-type production, and functionalization. Believing that producing ultrafine calcium carbonate with particle sizes of 0.02 to 0.1 μm, regardless of crystal form, and without considering dispersibility and activatability, can be applied in all fields such as rubber, plastics, ink, coatings, and papermaking is not realistic.
The particle size, crystal shape, specific surface area, oil absorption value, main content, and other parameters should be proposed with targeted and distinctive requirements according to different uses, thereby better meeting the needs of various industries and users. Therefore, it is very difficult to evaluate different types of ultra-fine calcium carbonate specifically designed for various applications using a single unified standard.
【Copyright and Disclaimer】The above information is collected and organized by PlastMatch. The copyright belongs to the original author. This article is reprinted for the purpose of providing more information, and it does not imply that PlastMatch endorses the views expressed in the article or guarantees its accuracy. If there are any errors in the source attribution or if your legitimate rights have been infringed, please contact us, and we will promptly correct or remove the content. If other media, websites, or individuals use the aforementioned content, they must clearly indicate the original source and origin of the work and assume legal responsibility on their own.
Most Popular
-
Amcor Opens Advanced Coating Facility for Healthcare Packaging in Malaysia
-
ExxonMobil and Malpack Develop High-Performance Stretch Film with Signature Polymers
-
Plastic Pipe Maker Joins Lawsuit Challenging Trump Tariffs
-
Pont, Blue Ocean Closures make biobased closures work
-
Over 300 Employees Laid Off! Is Meina Unable to Cope?