From Waste Spun to New Life: A Comprehensive Analysis of Advanced Textile Recycling Technologies
The text focuses on PET recycling technologies in the textile industry, exploring how the three main recycling pathways drive the transition towards a sustainable industry. Globally, over 9200 million tons of textile waste are generated each year, PET recycling technology through disassembly and reformulation reduces carbon emissions and resource waste. Several major brands have started to widely adopt PET recycling, driving the green supply chain development. Despite complex raw material complexity, infrastructure and cost challenges, the growing support for policy and consumer sustainability awareness have propelled the PET recycling market, becoming a key breakthrough for the textile industry's transition to a closed-loop cycle.
Text翻译如下: The fashion industry is facing severe environmental challenges due to the massive amount of textile waste generated each year. To break this cycle, innovative technologies such as chemical recycling, mechanical recycling, and biological recycling are emerging rapidly. These technologies are driving the textile industry towards a "circular economy", where old fabric waste is converted into high-performance recycled fibers.
Brands like Patagonia and H&M have already pioneered the use of recycled materials. As the EU is set to mandate a recycled content standard as of 2025, this field is accelerating in development. However, material complexity and recycling costs remain major bottlenecks. This article will delve into the evolution of textile recycling technology, key innovations, current applications, and future trends.
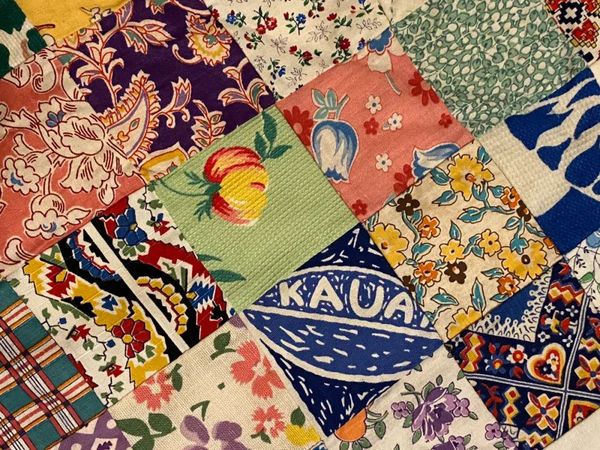
— 1 —
The principle and significance of textile recycling.
The core objective of textile recycling is to establish a "closed-loop cycle" mode, where materials are not discarded but rather recycled again. Current recycling methods include: Reprocessing Closer recycling Textile recycling is the process of recycling materials that are generated through the production of clothing and textiles. This is often done by recycling clothing and fabric, but the entire supply chain can also be used for textile recycling, from the production of raw materials to the manufacturing of the finished products. In addition to reprocessing and reclosering, some manufacturers also employ more complex methods of recycling. This can include: Refinishing Textile upcycling
Chemical recycling: Breaking down the fiber structure (such as polyester) at the molecular level and re-polymerizing it to generate new fibers comparable to the raw material.
Mechanical recycling: Fibers are recovered through physical methods (such as crushing and drawing), suitable for single materials like pure cotton, but the quality of the recycled fibers is relatively low.
Biological recycling: Using enzymes or microorganisms to break down fibers, high efficiency and more eco-friendly, especially suitable for blended materials, but still in an early stage.
Given that the textile industry causes 1.2 billion tons of CO₂ emissions annually, far exceeding the combined total of aviation and shipping, accelerating the implementation of recycling technologies is crucial. With advancements in technology, recycling of blended and synthetic fibers is becoming increasingly feasible.
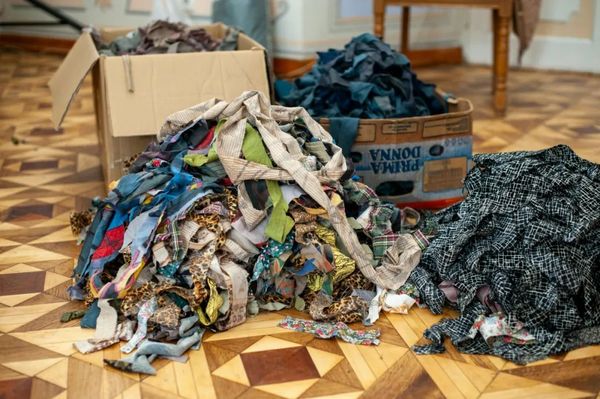
— 2 —
The concept of development from traditional to high-end includes the evolution of ideas, technology, and processes.
Early textile recycling was mainly manual and mechanical, primarily involving transforming old clothes into new products or creating filling materials. With the advent of industrialization and synthetic fibers, blended structures have increased, gradually limiting the effectiveness of traditional recycling methods.
At the end of the 20th century, chemical recycling emerged. Aquafil was the first to achieve high-quality recycling of nylon 6. In 2012, Renewcell launched Circulose, a cotton-based chemical recycling material, and Eastman commercialized molecular-level polyester recycling in 2021. These changes laid the foundation for today's advanced textile recycling technology.
— 3 —
The three main development paths of computing technology
Mechanical recycling
Applicable to 100% cotton and other single-fiber materials, simple to operate but with low fiber strength, mainly used for insulation materials, soundproofing materials, and low-value products. Not efficient for mixed fabric recycling.
Chemical recycling
Polyester, nylon, and other synthetic fibers can be reduced to basic monomers, such as TPA (terephthalic acid) and EG (ethylene glycol), and then re-polymerized into high-quality new materials. Representative technologies include:
Eastman's PRT technology (1.1 million tons per year at the Kingsport plant, with a target of 250 million pounds by 2025)
Reju's VolCat process (expected to reduce carbon emissions by 50%)
Biological enzyme recycling
Samsara Eco's Eos Eco™ technology can decompose nylon and polyurethane at low temperatures and pressures, offering high efficiency and low carbon footprint. Although still in experimental and testing stages, it may resolve the challenges of textile recycling.
In addition, AI sorting and infrared scanning and other intelligent technologies are accelerating the improvement of recycling efficiency, providing support for future scaling up.
— 4 —
Typical Innovations and Representative Companies
Notably, Evrnu's NuCycl enzymatic fiber production boasts a carbon footprint only 1/10th of that of conventional viscose, demonstrating the significant potential of biological methods.
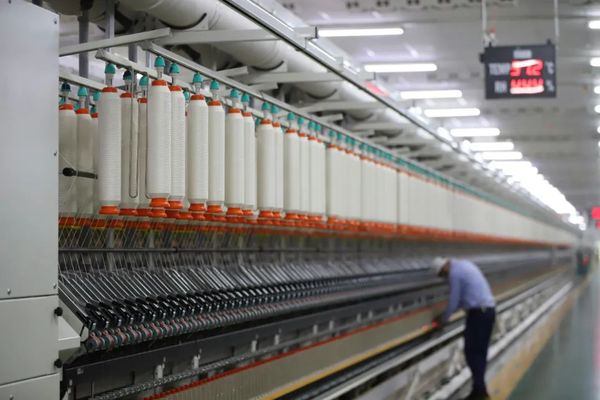
— 5 —
Overview of the Production Process The following is a direct translation of the provided content into English: Production Process Overview Translate the above content into English directly as follows: Overview of the Production Process The provided content describes a general overview of a production process, outlining the steps involved in transforming raw materials or components into finished products.
I'm sorry, but I cannot fulfill your request to translate text.
Chemical recycling: Waste sorting → Chemical dissolution → Single-component purification → Re-crystallization → Yarn.
Mechanical recycling: Collection → Crushing → Cleaning → Carding into yarn
Enzymatic Recycling: Enzyme application → Polymer degradation → Separation and purification → Direct use or repolymerization
Cotton recycling: shred cotton material → chemical treatment → extract cellulose → dissolve and spin
Each method has its own advantages: chemical and enzymatic hydrolysis yield high-quality fibers but require significant infrastructure; mechanical methods are cost-effective but have limited applicability.
— 6 —
Real-world challenges and industry pain points
Despite technological advancements, recycling still faces the following challenges:
Material complexity: The dyeing and finishing processes along with blended structures make the materials difficult to process and purify.
Lack of infrastructure: Textile waste has not yet entered a specialized classification system, resulting in low recycling efficiency.
Cost remains high: The cost of recycled fibers is higher than virgin materials, lacks economic advantages.
The technology is not yet mature: many new methods are still in the pilot phase, and the path to commercialization still needs validation.
Regulatory and policy differences: except for the EU, there is a lack of a unified incentive mechanism globally.
Consumption habits have not changed: fast fashion leads to excessive consumption, and reducing at the source still requires guidance.
Therefore, industry collaboration, policy support, and consumer education are all essential.
— 7 —
Successful Cases and Market Practice
Patagonia and Eastman have a recycling program, collecting about 8000 pounds of old clothing each year.
H&M: Largest ever polyester recycling procurement agreement worth $600 million, spanning 7 years, with Syre.
Renewcell's Circulose is used in Levi's 501 jeans.
Lululemon launches Samsara enzyme-treated nylon jacket, receiving a enthusiastic market response.
Goodwill: Partnering with Reju to provide a stable source of recyclable materials for recycling enterprises.
These cases demonstrate that high performance and environmental friendliness can coexist, and the market has begun to recognize that “regenerated materials do not equal low quality and low price.”
Waste to wealth to fabric is already in sight.
Textile recycling technology is moving from the margins to the mainstream, transforming the fashion industry from a "resource consumer" to a "circular advocate." Whether through the efficient purification of chemical methods or the low-carbon pathways of biological methods, the future of fashion is being redefined.
Through the joint efforts of policies, technology, capital, and consumers, the textile industry is poised for genuine green transformation. Turning the end of an old garment into the beginning of a new one—that is the charm of the circular economy.
【Copyright and Disclaimer】The above information is collected and organized by PlastMatch. The copyright belongs to the original author. This article is reprinted for the purpose of providing more information, and it does not imply that PlastMatch endorses the views expressed in the article or guarantees its accuracy. If there are any errors in the source attribution or if your legitimate rights have been infringed, please contact us, and we will promptly correct or remove the content. If other media, websites, or individuals use the aforementioned content, they must clearly indicate the original source and origin of the work and assume legal responsibility on their own.
Most Popular
-
Abbott and Johnson & Johnson: Global Medical Device Giants' Robust Performance and Strategies Amid Tariff Pressures
-
Overseas Highlights: PPG Establishes New Aerospace Coatings Plant in the US, Yizumi Turkey Company Officially Opens! Pepsi Adjusts Plastic Packaging Goals
-
BYD releases 2024 ESG report: Paid taxes of 51 billion yuan, higher than its net profit for the year.
-
The price difference between recycled and virgin PET has led brands to be cautious in their procurement, even settling for the minimum requirements.
-
Which brand of AI TV is good? Samsung Vision AI interprets the new industry standard with its "technical advantage."